Questions from the Mailbag: Concrete, Installation Concerns
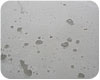
Concrete slabs to receive a floor covering need to be free of any type of sealer or compound. One of the best ways to check a slab is to flick some water onto it. If the water is absorbed, it can be assumed the slab is ready.
It’s never a bad idea to ask questions, especially for something that can be as tricky as installation. You can learn new techniques and time-saving ideas by asking the right questions about the job. So let’s look at answers to some commonly asked questions from my mailbag. As always, I appreciate your feedback.
Q: Why are flooring manufacturers against installing over sealers, curing and parting compounds?
A: ASTM F-710 states that concrete slabs should be free of residues, including sealers, curing and parting compounds. Let’s look at the intended uses of each of these products:
Sealers are designed for a walking surface of concrete to control dusting and not as an underlayment. Sealers are easily applied and very difficult to remove.
Curing compounds are designed to hold the mix water in concrete for hydration purposes. Curing compounds are supposed to degrade from the surface of the slab, over a period of time, either through oxidization or ultraviolet degradation, allowing foot traffic to walk the residual off.
The problem with curing compounds is that they are supposed to be applied in a very thin layer (1–1 1/2 mils thick). In many instances the coating is applied too thick and does not degrade in the allotted times, which prolongs the start of the concrete drying process, thus delaying the start of any flooring installations.
Concrete slabs with a curing compound need to be mechanically abraded to be sure the residual is gone, especially along walls and where foot traffic is minimal. Even worse is a combination cure and seal product that is difficult to remove. These are normally solvent-based products and when applied too heavily will retain the residual solvent for a long time. These types of products have also been known to attack flooring installation adhesives, even one year after a flooring product was installed. The concrete industry is gradually discovering that wet curing works better than a curing compound.
Parting compounds are used primarily in concrete tilt-up construction. These compounds can be oil-, silicone-, wax- or soap-based. Also known as a “bond breaker” they prevent the tilt-up wall, which is poured on the surface of the slab, from sticking to the slab. Bond failures are caused by this residual not being removed from the slab surface.
All of these compounds should not be used or totally removed if one has been used previously. The comment made by some: “It is just one more substrate that is likely to fail” is appropriate.
Q: What are your thoughts on installing over a hard troweled concrete?
A: A lot depends upon what you are going to install over it. Hard troweled concrete presents a lot of difficult scenarios for the flooring industry. When drying concrete, a hard troweled surface will retard the drying of the slab. For bonding it is difficult to get a good mechanical bond. When using an adhesive like an epoxy or urethane adhesive it is imperative to have a surface that the adhesive can get a good hold to.
Q: What should the normal concrete surface temperature be for flooring installation?
A: More attention should be paid to concrete temperature than ambient temperature. A case in point is an installation where the contractor indicated the heat had been on for two weeks and the ambient temperature was in the high 60s, but the slab temperature was in the high 50s. The heat had only been on for a couple of days and the slab had had no time to warm up. Going over a slab this cold stands a good chance of failure due to a multitude of potential problems. The concrete temperature should be between 68°F (20.0°C) and 72°F (22.2°C) for a successful installation.
Q: What are the factors that cause underlayment joints to show through the finished flooring material?
A: With the quality of underlayments on the market today there are factors that have changed from some of the old methods of installation.
1. Acclimation is the most important. Not only on-site but acclimation of the skids in the warehouse. A skid can take up to 45 days to acclimate. It may be necessary to take the sheets out of the skid and allow them to acclimate prior to installation.
2. The edges of the panels need to be laid-up, with factory edges butted lightly.
3. Select the proper fastener -- 3d ring shank fasteners are the most recommended, but a narrow-crown staple can also be used. Do not overdrive the fastener.
4. Place the fastener within 3/8” from the panel edge and at the proper spacing interval.
5. Sand the joints to smooth and do not fill. The only filling that needs to be done is a joint that has an opening thicker than a credit card.
Q: What are your thoughts on full spreading an epoxy under a vinyl-backed sheet vinyl floor used under hospital beds?
A: The use of epoxy is greatly overrated. The main culprit in this scenario is the wheel on the hospital bed. There are two types of wheels used; one has a flat surface and the other has a rounded surface. The wheel with the rounded surface creates the highest compressive loading and the smallest footprint. This is exacerbated when the wheel is locked and when the bed is moved, causing the wheel to pivot, creating a shear between the material and the adhesive.
An epoxy adhesive will have greater resistance to this than an acrylic adhesive. Ask yourself, are the additional labor, costs of adhesive and finesse required for this type installation worth it?
Looking for a reprint of this article?
From high-res PDFs to custom plaques, order your copy today!