Successful Subfloor Preparation is Essential for Happy Customers
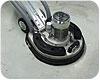
Floor grinders using dust containment systems with various attachments are really a necessity for anyone who does installation work over slabs on a regular basis. Photo courtesy Dave Gobis.
Installation success only happens with thorough subfloor and job preparation. Skipping a moisture test, not removing concrete curing or sealing compounds, not removing old adhesives, or not leveling a subfloor are sure steps to a costly job failure.
In this month’s column I will cover some of the current concrete subfloor issues and solutions the flooring installer faces each day. Proper installation methods over concrete surfaces are critical for success. These methods are constantly changing due to evolving enhancements to flooring materials, adhesives and construction practices.
Burnished or hard trowel finished concrete is a large and growing problem that we are receiving from the concrete industry. With the use of power trowels the concrete finishers are over-troweling the concrete surface, leaving a burnished surface.
Hard-troweled concrete is shiny and highly consolidated and presents several problems for the flooring industry. First, the highly consolidated surface severely slows the drying of the slab because the moisture is slow to pass through the consolidated layer.
Second, moisture testing that is done at the surface will yield low readings (false positives) due to the retarded moisture vapor flow and the short period of time the test is run.
Third, some adhesives, especially epoxies and urethanes, will not be able to achieve a good mechanical bond to the concrete’s surface. These types of adhesives are designed for excessive abuse and require an open pore in the slab’s surface to attain this bond.
Concrete curing or sealing compounds – ASTM F-710 states that if a curing, sealing or parting compound is to be used it should be removed. Problems begin as many flooring contractors do not realize that sanding with a buffer will not remove the compound. Sanding will only scratch the curing, sealing or parting compound.
Other installers believe that curing or sealing compounds will either walk-off or degrade from either UV exposure or oxidation. While this is somewhat true, the exposure does nothing to the pores of the concrete that is filled by this same compound. These compounds also slow the migration of moisture and retard drying.
This is another reason why surface moisture tests must be ground to open the pores of the concrete’s surface. Going directly over a curing or sealing compound is foolish. I have seen situations where the residual solvent in a heavily applied cure ‘n seal attacked the applied adhesive about nine months after the installation.
Buffing or sanding the surface of the concrete – Installers will give a concrete slab a quick sanding with an 16 or 24 grit open coat sandpaper, thinking they have taken care of anything that might prevent a good bond. On the contrary, sometimes scratching a latent substance that is present on the surface of the concrete will only allow it to de-bond faster from the concrete surface. Situations like these de-bond sometime after the slab is in use.
Poorly finished concrete – Poorly finished concrete is generally dusty and very absorptive. Dust will cause the adhesive to ball-up and also to dry too fast. Usually, concrete like this will require a primer to slow the absorption and drying time.
Latent substances on the concrete surface – Many times in new construction a lot of mud can be tracked onto the concrete surface. If the mud is clay-like or high in fines it can stick to the surface like it is part of the concrete. A solution for this would be to use a buffer sander to remove this laitance, or a layer of weak powdery material on the surface.
Concrete mitigation treatments – Many contractors are automatically planning for moisture treatments from past experiences with moisture. When an installer arrives at the jobsite, make sure he is aware if the slab has been treated for moisture. Otherwise he may disturb the ongoing mitigation treatment.
The next thing the installer needs to be aware of is if the slab is non-porous and needs to be treated as such. Other factors the installer should be aware of include whether the job will feature a specialty flooring or companion adhesive that needs to be installed over a porous substrate.
Concrete to have epoxy applied – Some slabs are either going to have an epoxy adhesive used under a resilient flooring product or have an epoxy coating applied. In either of these situations it is necessary to be able to achieve a good bond between the adhesive and the substrate.
Choosing the correct CSP profile – When should you abrade the concrete surface? For proper bonding of concrete overlays and coatings, it’s important to give the surface the correct concrete surface profile, or CSP.
To help contractors make this assessment, the International Concrete Repair Institute (ICRI) has developed benchmark guidelines for CSP-a measure of the average distance from the peaks of the surface to the valleys. They range from CSP 1 (nearly flat) to CSP 9 (very rough). As a general rule, the thicker the overlay or topping, the more aggressive the profile needs to be. A skim coat, for example, may require a light CSP of 2 to 4. For thicker self-leveling or polymer overlays, acceptable profiles generally range from CSP 4 to 6. Achieving surface profiles in the higher ranges often requires roughening by shotblasting or scarifying.
With existing adhesives, the majority of the adhesive must be scraped to a thin residue before shotblasting to prevent the shot from gumming up or bouncing off the surface of the adhesive.
The purpose of surface preparation is to provide sound, clean and suitably roughened surfaces on concrete substrates. This process includes the removal of unsound concrete and bond-inhibiting films, strength verification, opening the pore structure and establishing profiles suitable for the application of the specified flooring system.
Looking for a reprint of this article?
From high-res PDFs to custom plaques, order your copy today!