How to Remediate a Cupped Wood Floor
The first step of remediating a cupped floor is to determine why the floor cupped.
There are basically three causes for a floor to cup:
- Extra and/or excessive moisture affects the flooring from below.
- Drier flooring that gains moisture dictated by a more humid environment after installation and no field spacing which was created during installation for the expected expansion.
- Flooring dries from the surface while the back or bottom of the flooring remains at a more constant moisture content.
Another much less common cause involves thinner flooring that has been re-sawn before final shaping. Internal drying stresses such as case hardening can result in cupping. Again, this condition is very rare; I have only noted one or two cases where drying stress was the suspected culprit.
With the typical cupped floor, the culprit is cause # 1: extra or excessive moisture affecting the flooring from below. That is the crawl space is too wet or too humid, the slab is wet or not properly cured, or the subfloor components are wet. A moisture event such as blowing rain through an open window or door will result in cupping, as will a plumbing leak such as an overflowing dish washer or ice maker valve. With the water event, even though the face is wetted most of the water seeps under the boards and remains there until a slow drying process can be completed.
Other more subtle causes involve air infiltration where warm outside humid air comes into contact with cool conditioned air and results in high sustained humidity or condensation as the dewpoint temperature is reached. These conditions are most likely found where heavy cooling loads are present such as the sunny southern or midwestern states with humid summers. Inadequate caulking around doors, open framing spaces from the attic to the second floor framing and outside brick veneer can contribute to cupping. Crawl space homes often have high sustained relative humidity in the crawl space. The warm outside humid air is supplied by foundation vents and the space below the home is cooled by duct work so the resulting temperature and humidity approaches or reaches dewpoint (Photo 1). A plastic ground cover can help keep soil moisture in the soil but not the air flow. I have seen a second floor cupped from air infiltration and not the ground floor (Photo 2). I have seen all kinds of moisture issues in crawl space homes from flooded earth (Photo 3) to wet dripping ducting and to ducting half-filled with water.
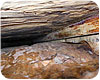
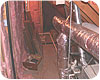

In all these cases the source of the moisture must be identified and stopped. Then the remaining abnormal or moisture source should be removed and dried. In some cases, if the cupping was not severe the flooring may flatten to an acceptable level with minor gapping after drying. Remember the flooring has lost moisture so some shrinkage will result. Before any repair or remediation the flooring should be checked for looseness. The stress from cupping and expansion can certainly loosen the fasteners. If no looseness is found the options are: live with the resulting condition, re-sand and refinish, remove and reinstall and or replace. If the flooring is loose, reinstalling the dried flooring is an option along with replacement. Another remedy is general face nailing of the loosened boards before refinishing. An older floor will be a likely candidate for this repair. If the event initiated an insurance claim and repairing the existing flooring is chosen, all parties involved must understand the expected performance of the repair and be patient as the drying and ultimate repair may take months. A quick fix will likely not be acceptable. Some permanent gapping and occasional noises may be the result. The time for the repair is generally after the dried flooring system has gone through a heating season. Either the spring or fall is the best time, when the flooring is at an average environmental condition.
The #2 reason for cupping is: flooring that gains moisture dictated by a more humid environment after installation. This can be an acclimation issue or if flooring was overly dry at delivery. Most of the time, the flooring cups gradually over time to a particular degree of cup and doesn’t get any worse (Photo 4). The moisture content of flooring at this condition is normal for the geographical area and has little difference from the face to the back of the flooring. The flooring will also be tight together (Photo 5). Most of the way to determine if the cupping is permanent is to allow the flooring to go through the heating season. Cupping that remains or subsides only a small amount will be considered permanent.
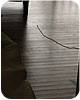

Options for repair are similar to the other cupped floor. But the cupping will likely not be as severe. Living with the condition is one option but the cupped floor is unsightly and, if a new floor, is not likely to be chosen. This cupping will gradually subside with time and multiple seasonal changes but may not completely go away. The most often repair choice is to re-sand and refinish the flooring. The same spring or fall time line is suggested along with checking the flooring for looseness before starting the repair.
Causes #1 and #2 are related to expansion which can also lead to buckling. If a floor has buckled, that is it has released from the subflooring/substrate, replacing or removing and reinstalling the area will be necessary (Photo 6). Any new replacement flooring should be checked for moisture and be at or near the moisture of the surrounding sound flooring. For a floor that is tight with no buckling or looseness and cupping near 3/64” or .05”, providing expansion relief will be necessary to save the floor. Cutting out a run every 36” to 40” to allow the flooring to relax and flatten over a period of time. Sanding a floor that is cupped 3/64” or greater will likely remove more than 1/16” of the wear surface. This may not be a problem with 3/4” thick flooring, but thinner flooring or engineered flooring will be at risk of sanding through the edges of the surface or breaking off the groove edge.

The #3 reason for cupping is: drying from the surface. This is the result of the flooring being at a higher moisture content than the installation’s environment. The likely cause of this condition is storage in a too-wet environment or being manufactured at an elevated moisture content. As noted with this condition drying occurs so that resulting gapping will be present. For a solid floor as flooring acclimates to the space the initial cupping will subside and gapping will be the issue of the finished floor. In this case allowing the flooring to complete a heating season will likely fix the cupping as the elevated moisture will be removed by the heating and the flooring will flatten. The only issue will be whether to repair the gaps or leave the flooring as is. An engineered floor under these conditions of drying and cupping will likely have other issues such as excessive cracking of the face veneer and/or separation and fracturing in the veneer layer so re-sanding is often not an option for remediation.
In order to help a severely cupped floor flatten after the moisture source has been fixed or removed, sanding the finish off can accelerate the drying. The sanding direction should be across the floor so that the edges are not sanded aggressively. The objective is to remove most of the finish, about 70%, so the flooring can better breathe and evaporate moisture. Adding air movement with fans can facilitate additional drying. Later as the refinishing procedure begins the first sanding passes should be at an angle to flatten the floor. The more severe the cupping, the greater the angle of attack, up to 45 degrees, during the initial sanding (Photos 7, 8, 9, 10, and 11). A second pass in the opposite direction may be necessary if the first pass doesn’t flatten the floor. Use the same grit of paper on each pass and after the flooring is flat straighten the sanding with this same grit making a pass in the direction of the flooring. Then proceed as usual with the refinishing. If face nailing is necessary to reduce movement and noises, pick the open grain of the wood to hide the nails/cleats/ trim screws with filler.
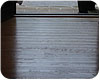
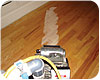
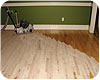
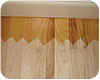
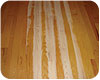
Many times a cupped floor can be remediated and repaired without complete removal. For severely wetted flooring this becomes an “iffy” situation and insurance is involved so replacement is the most often used option. But for the cupped floor that is cosmetically objectionable addressing the cause and establishing a proper environment can likely allow the flooring to be saved and repaired. As always, set the proper customer expectations for the issues related to the repair and the time involved in the repair. Again, a quick fix will not be a long-lasting and acceptable remediation. Thanks to Wayne Lee, Cardinal Hardwoods, for his photos of the sanding procedures, and Craig Dewitt, RLC Engineering, for photos of environmental issues.
Looking for a reprint of this article?
From high-res PDFs to custom plaques, order your copy today!