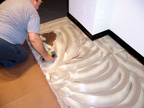
What are the responsibilities of the commercial flooring installation contractor when a suspected material quality defect is noted? This is a question I have heard a few times during my 25-year career in the resilient flooring industry. Unfortunately, the question is often asked long after the project has suffered serious delays, or worse, the project has been completed and the installation is unacceptable. At this point the situation often becomes unpleasant for all involved.
The first and most important step in any construction project is to ensure that all parties involved have current, signed contractual agreements in place that obligate each to follow certain pre-set guidelines for a particular project. If a flooring contractor encounters product that he believes is substandard quality during the installation, under typical contractual relationships the contractor needs to report his concern through the direct business chain, to the general contractor, as well as the product supplier. It is then the flooring contractor's responsibility to act in a fiduciary manner and determine whether or not to continue working on the project.
At that point a number of factors should be taken into account to determine whether to stop work on a project:
• The severity of the alleged defect. Can it be resolved with a minimal amount of additional labor or material?
• The construction project deadline. Will a work stoppage result in significant, minimal, or no loss of time? Will the installer remain on track to complete the project within the approved time?
• The overall end result. If the installation continues, will the final result be aesthetically acceptable and will the product perform as it was designed to perform?
Realistically, some of these questions are beyond the scope of the flooring contractor. That's why it is best for all parties to work toward a mutual agreement on how best to address the situation.
Communication among distributors and product manufacturers sometimes can result in the use of mitigation tactics, if necessary, but this is not a technique that is usually top of mind for a flooring contractor. In most cases true defective material may be limited in the production run of material. Involving the manufacturers' technical departments, given their familiarity of the product, could help to sequester the true defective material from product that will perform according to design. Information swapping during these situations helps to control costs and keep projects on schedule.
It is the flooring contractor's responsibility to retain representative samples that clearly demonstrate the nature of the alleged quality defect. The contractor also needs to collect all documentation including invoices and related information. Detailed records of additional incurred expenses need to be maintained for possible review at a later time.
Upon notifying the product supplier of a potential product defect, these product samples along with documentation, need to be forwarded through the distribution chain, ultimately to the product manufacturer. Instructions, as given by the product supplier, need to be followed in a timely manner. Again, the quicker the flooring problem is identified and addressed, the quicker it can be resolved.
In this age of fast-track construction I find it amazing that some flooring contractors follow entirely different business practices when it comes to aggressively pursuing revenue-generating activities versus possible revenue-eroding delays, and avoidance tactics when it comes to communicating negative scenarios. Timely notification and follow-through helps control unexpected expenses for all parties, ultimately preserving margins and fostering business goodwill and profitability.
Report Abusive Comment