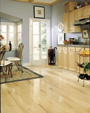
In our industry, hardwood flooring has always been perceived as a universal floor covering for most residential applications. The limitations for potential hardwood applications are minimal at best. And areas of the home that were once considered off limits to our industry are increasingly deemed quite suitable for a variety of hardwood flooring products.
The long-standing belief that water and wood don’t mix still remains true. But who says that we can’t find a way to reconcile wood floors with so-called “wet” areas of the home? For instance, powder rooms equipped with sinks and commodes are now common recipients of hardwood flooring installations. A decade ago, hardwood floor installations began creeping into kitchens and the adjacent breakfast areas of the home. Since that time, kitchen hardwood applications have moved steadily up the “installation chart” of desirability.
The key to success in such environments requires what I call a “water patrol” policy. Leaks, if undetected or ignored, can damage any flooring product. Water and wood can exist in harmony as long as protective boundaries are established between the two. After all, without water, there would be no trees. With that in mind, an amicable reunion seems quite fitting.
Statistics point to the fact that hard surfaces, in general, continue to consume more internal territory of today’s homes. Designers learned long ago that a continuous room-to-room flow, or theme, in floor covering dramatically enhances the perceived size of the overall area. Unlike competing floor coverings, hardwood floors do not promote an unwanted contrast. Rather, they create a desired blend that serves as the universal path between areas of the home.
Unfortunately, due to certain widely held misconceptions, some skepticism persists regarding the versatility of hardwood flooring. Old-school notions about tedious hardwood maintenance procedures definitely are outdated. And it’s high time that consumers be educated about the much easier maintenance regime required by today’s wood floor products.
For the most part, limitations on the use of wood flooring are self-inflicted. Often, the salesperson simply refrains from promoting hardwood for kitchen installations. Resisting the attractive potential of hardwood in their sales presentations is like taking customer’s food order without allowing them to review the full menu. Salespeople should strive to present the practical aspects of hardwood in the kitchen. By doing so, you can change your image from a “fast food server” to a “gourmet chef.”
The kitchen has actually become one of the most prime locations for hardwood installations. Assist the consumer in adding a little “spice” to her lifestyle. And for your information, this particular “ingredient” is no longer a “secret recipe.” Historically, kitchens have always been the traditional gathering place for verbal exchange during the family dinner hour. A “hot” meal served over the “warmth” of a hardwood floor is a picture perfect “place setting.”
The following recommended guidelines will not only add the needed “flavor” to your kitchen installations but also dramatically reduce the chance of turning the hardwood experience from “sweet” to “sour.”
Kitchen installations require a urethane-finished wood product. A wax-finished product or use of an acrylic polish that is not recommended by the manufacturer may eventually succumb to spotting wherever water drops from the dishwasher and/or sink contact the wood floor. Acrylic-impregnated products are also susceptible to this problem.
Check for clearance with the existing dishwasher in the event future repair or replacement is required. Always recommend that the consumer replace the dishwasher if it is in questionable condition or likely to need future repairs.
Also, refrigerators equipped with icemakers should be checked for leaks before the installation commences. Advise the customer of your findings and document them. Special care should be taken in the removal of all appliances as well as their repositioning once the floor is installed. Protect the new wood floor and advise the customer of the proper procedures required for future removal of heavy appliances.
Exterior doors require a tight seal threshold. Remove the threshold for the installation. Once the threshold is reset, the door will likely require cutting to accommodate the additional height elevation of the finished floor.
As with all hardwood installations, adequate room for expansion is a critical requirement to allow for seasonal changes in both temperature and relative humidity. Remove the existing baseboard. Hardwood requires a gap approximately 3/4 of an inch along the entire perimeter of the kitchen. Depending upon the thickness of the baseboard, additional shoe mouldings or quarterround stained or colored to match the baseboard may be required. Definitely, the toe kick of the cabinets will require additional trim.
Smooth transitions between the kitchen flooring installations are always desired by the customer. Addressing those concerns from the beginning in your bid and arriving prepared to install these additional trim pieces will not only fully complete the installation but also reduce the risk of the customer withholding final payment.
Distribute and review literature that outlines normal maintenance procedures. Provide the initial supply of the maintenance product specified by the manufacturer for the urethane finish. Periodic routine maintenance enhances the performance of the hardwood floor and the finish. Felt pads are highly recommended on items such as tables or chairs that will require movement on a daily basis or for routine cleaning.
Hardwood floors are engineered for a lifetime of use. But that definition of “lifetime” truly depends upon the customer, proper maintenance and -- most importantly -- the environment. All urethane-finished wood floors will require recoating at some point. Obviously, the floor can also be re-sanded in most cases. The re-sanding option typically is at the customer’s discretion for reasons of color change and/or excessive indentations or deep scratches.
By following these simple recommendations, kitchen installations will continue to be a “hot spot” for our industry. Wood or Wood Knot just wants to make sure that you maintain “cool” customers and satisfy your “hunger” pains for additional quality hardwood flooring installations.
Report Abusive Comment