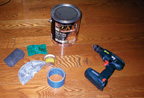
The dealer/contractor has always been considered the front-line representative of the hardwood flooring industry. Consumers continue to be tantalized with the multiple potential products available from our progressive hardwood flooring manufacturers. The buyer relies upon our expertise and advice before making a buying decision that is intended to last a lifetime. There is definitely a fine line between overselling and understanding the fundamentals and characteristics associated with all hardwood flooring. Synthetic floor covering products must be consistent in visual appearance. Natural hardwood flooring offers the customer an installation composed of variations that cannot be duplicated. The opportunity to purchase an "original" vs. a "reprint" has always been a determining and driving force for our industry.
There is nothing more satisfying for today's floor covering consumer who is exposed to the redeemable traits associated with a hardwood of choice installation. Unfortunately, these same individuals truly don't always understand a "diamond in the rough" concept as well. Obviously, I am prejudiced, but the membership is this "club" is not only "open" but also growing with no "closure" in sight.
The mere quality of serviceability alone can withstand an unwarranted pounding from a careless end user. Through my years of experience, I have seen installations that have been neglected, abused and begun to show signs of deterioration. Indeed, these installations might be considered the "ultimate challenge" to the hardwood flooring contractor. In most of these circumstances, both the contractor and the hardwood flooring installation itself are eager challengers to the task at hand. Maybe some boards will have to be replaced, but maybe not. A qualified contractor utilizing good judgment and then explaining the process to the customer will ultimately prevail.
Of course, proper care with minimal maintenance can preclude the need for total restoration of any hardwood flooring installation in a HVAC-controlled environment. Depending upon usage, the eventual requirement for recoating the installation with a compatible system renews the protection for the everyday normal wear and tear.
As an industry, the local participating contractor must provide customers "after-installation" services. There are three distinct classifications in the service-after-the-sale market. They are as follows: 1. Service required by the contractor responsible for the installation. 2. Repair requirements that pop up after a substantial amount of time has passed or failure by the initial contractor to respond to the customer request for service - warranted or not - within a reasonable time. 3. Conditional changes from usage, or environmental or accidental mishaps.
Determining responsibility by the original contractor via the telephone will never replace the job-site inspection. You will definitely be considered guilty by the homeowner. My suggestion: Represent yourself now before you are required to have legal representation later.
Depending upon the ability of the contractor, repairs shouldn't be classified as a negative confrontation but instead a positive experience. If the contractor is at fault, the installer and/or finisher responsible for installation should be required to return to the job site for the necessary adjustments. Notice that I have removed the word "repair." Repairs send a message that is perceived as possibly being temporary. The level of acceptance by the homeowner increases with a timely response under most circumstances. These recommendations are for adjustments vs. unwarranted board replacement.
Scratches. Unfortunately, even meticulously kept homes are not exempt from the potential occurrence of scratches. The contractor needs to qualify their severity. This will determine the appropriate adjustment process.
I have always called these superficial events "memories." I am the proud grandfather of six and my home has more than its fair share of memories. And yet, the overall appearance of my floors still delights me.
There are multiple tools at our disposal for adjusting the installation. Scratches can be isolated with the use of a quality blue tape around the perimeter of the board. Then, the board should be lightly abraded with a piece of fine steel wool (for a solvent-based finish touchup) or a synthetic-based scouring pad (for a water-based application). Remove any dust with a tack rag. Apply the same luster of finish over the isolated board, and remove the blue tape. Protect the area until the finish has dried.
On worn finishes in heavy-traffic areas, return to the job site after the first coat of finish has fully dried and lightly abrade the area to tone down the luster of the new finish so that it will visually blend with the surrounding boards. The frequency of scratches may qualify the installation for a compatible recoating.
Indentations and splits. Many times, boards can be filled and "spot stained." On small indentations, the use of a compatible ambering type of polyurethane floor finish can be applied with a ketchup-type dispenser into the indentation and leveled off with a small plastic putty knife. Then, remove the excess around the "wound" with mineral spirits.
Another method is to fill the void with fillers that are already shaded similar to the existing stain of the installation. Even when the growth rings or "veins" are damaged, permanent markers can be used to recreate the continuous line the vessels once contained. Crayons and or water paints can also be used for this purpose.
These touchups will require urethane protection as well. Always have a rag lightly saturated with mineral spirits for toning down the area. Going a little lighter in color usually is better going too dark.
Squeaks. Utilize 11/4-inch decking screws from below between the joists and fasten directly into the subfloor and hardwood flooring strips and/or planks. Avoid facial repairs with nails from above. If you are unable to access the area below, drive single cleats between the boards and set with a nail punch and then putty with appropriate filler. Pneumatic brad-face nailers can also be utilized. They "self" set and, if discreetly installed, can normally get lost in the grain. If this fails, putty with filler.
Wood or Wood Knot acknowledges those dealer/contractors that are ready, willing and most of all able. Start today by "adjusting" your outlook so you, too, are capable for "adjustment" tomorrow. Small repairs in hardwood floors are really "knot" so bad.