The Top Five Tile-Related Complaints--Again

Do any of the following complaints sound familiar?
"Help! We just had a party and our five-year-old tile floor is cracked all over."
"My contractor just put in a wheelchair-accessible shower for our daughter and now water is leaking through into the basement."
"The contractor says my tile is growing and now I have a big hump in the floor. How do I make it stop?"
"My grout is all soft and powdery, and it comes out when I vacuum. The contractor came out and put water in it and said it would make it harder."
I've gleaned these comments from calls I received the week before I wrote this article. Sadly, I hear nearly identical complaints almost every week. The worst part is all of these problems are installation related, which can make a tile professional like me downright depressed.
So, why all the problems? In probably 98% of the instances, it is - pure and simple - failure to follow instructions and observe established installation guidelines. I never thought, during my nearly three decades as a contractor, that the day would come when I would agree with that statement. However, after three years of fielding tile-related complaints in my position with the Ceramic Tile Education Foundation (CTEF), I must report - albeit sadly - it is true.
Granted, as a specialty flooring retailer, you won't be going to the job site to lay tile for your customers. However, if a problem crops up, you can count on hearing from the client. By being aware of the most common installation-related pitfalls, you can bring your influence to bear on your installers and impress upon them the need to follow accepted procedures and do the job right the first time.
In compiling a list of the top five most-common tile failures, I consulted with Bob Daniels, executive director of Tile Council of America (TCA), and Noah Chitty of TCA Technical Services. Combined, the three of us handle approximately 5,000 calls and e-mails a year, up from 3,000 only two years ago. Surprisingly, we all agreed on the top five problems, although we differed somewhat in ranking them. So here, in random order, are the top five tile-failure calls we receive.
Floor Prep. Substrates must be clean - meaning free of all foreign matter, paint, curing compounds, dirt, and anything else that interferes with bonding. One contractor actually sent me a tile with paint overspray and sawdust imbedded in the thinset. He wanted to know why it didn't stick to the substrate.

Coverage and Type of Thinset. In the tile industry, you're sure to encounter a multitude of substrates, tile types and installation conditions. Happily, there is a thinset mortar available for every application - so use the right one! Manufacturers don't make six to 10 types just so that they can charge different prices. They are different products with different properties and recommended uses.
Once you've obtained the proper product, you'll need proper coverage. This is important in the installation of all tile types and particularly critical when large-format tile is used. The requirements are 80% evenly distributed on interior substrates and 95% on exterior or wet areas. The notch-size instructions listed on the bag of thinset are general recommendations, not gospel. The manufacturer has no way of knowing if you will be installing lug-back, waffle-back, ribbed-back, or some other type of tile.
Most products contain a reference to ANSI A108, which is where you will find the rest of the requirements for proper installation. Encourage your installers to practice directional troweling on large-format (larger than 8 inches square) tile and you will be far less likely to get customer complaints about cracked tile or broken corners.
Movement Accommodation Joints. A thorough discussion of this subject would take many pages to address. Tile industry icon Bob Young wrote an article some years back that said many tile installations are held down by the "Three Gs"- God, Grout and Gravity. However, even the Three Gs have little influence on the integrity of an installation if the tiles have nowhere to move.
All building materials move, and each type moves at a different rate. This is a problem that must be considered in every installation, regardless of size.
Packing grout into the wall line at the perimeter of the room is a leading cause on the failure list. A minimum 1/4-inch joint along the entire perimeter of the installation must remain free of grout, backerboard and/or thinset.
Where there is no wallbase, some backer rod and caulk may be used to fill the gap at the perimeter. If the installation is regularly exposed to sunlight, movement joints must be placed in the tile work at no greater than 12-foot intervals. Complete recommendations are contained in the TCA Handbook under detail EF171. Fail to follow these guidelines and even the Three Gs can't save you.
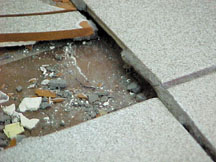
The first time, the installers didn't realize that they needed waterproofing and, once they became aware of the requirement, incorrectly put it in. Waterproofing should be considered for any use of tile that will be subjected to more than intermediate moisture, such as an occasional spray.
Actually, this is an aspect of tile installation where manufacturers have excelled - in particular, with trowel-on systems, sheeting and even preformed curbs, jambs and entire shower bases. Even so, the skill level required for this work goes beyond what's needed to install floors.
To work as designed, all of these wonderful waterproofing systems must be properly installed. The margin for error is zero. If one does not install vapor membranes behind walls where required, or drives nails through the bottom 8 inches of the shower pan, or nails backerboard curbs through the membrane, he won't have to wait long before the dissatisfied customer tries to relieve him of his wallet.
Improper Installation of Backerboards. All the benefits of using backerboards are rendered useless unless specific, yet simple, instructions are followed. All backerboards for floor use require a leveling bed. Let me repeat that: a leveling bed is required!
The purpose of thinset under the panel is not confined to bonding. Rather, it's also designed to provide a solid backing surface that's free of voids. Some backerboard manufacturers specifically do not want the panel bonded; they recommend dry set mortar for that purpose.
Proper fasteners are critical because it is their job - not that of the thinset - to secure the panel. Minimum head diameter for such fasteners is 3/8 inch. This means no drywall screws! Galvanized roofing nails, however, are acceptable. When using pneumatic nailers, the head of the gun must be firmly placed against the backerboard surface before the tripper is pulled. This helps prevent the panel from resting solely on the ridges or, even worse, riding up the nail.
Gaps should be left between sheets and treated per recommendations. If appropriate gaps are not in the supporting wood panel, edge swelling may push the whole backer board off the floor resulting in tile cracks at the sheet perimeter.
Finally, backerboards are nothing more than backerboards. They provide no structural value. If you try to make them part of the supporting structure, the tile may crack due to the building stresses that have been applied to the panel. Subfloor recommendations are minimums. If the subfloor has been open to the weather, other measures may be warranted beyond the installation of backerboard.
The DOs and DON'Ts of tile work are legend. Cataloguing them all could fill volumes, but the ones outlined here are definitely at the top of the list. Following the established guidelines of the TCA and ANSI handbooks will result in successful installations. These documents are written and approved by the industry. In addition, the CTEF offers courses based on these and manufacturers' proprietary methods.
Looking for a reprint of this article?
From high-res PDFs to custom plaques, order your copy today!