Ceramic Mastic: Call it What You Will So Long as it Sticks
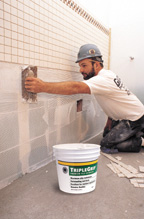
Whether you call the product "mastic," "adhesive," "stick-um" or -- as some old-time mud installers call it -- "chewing gum," it serves a wide variety of ceramic construction purposes. Mastic is fast, labor saving, inexpensive, and is ready to use as supplied in pails.
The American National Standard Specifications for the Installation of Ceramic Tile, ANSI A 108, lays out the method for installing ceramic tile with organic mastic. In section A-4.2, ANSI points out that use of organic mastic over gypsum board or gypsum plaster is not approved if used in wet areas. In wet areas, water-resistant (WR) board must be used.
Adhesive Application. Though seldom done in actual practice, ANSI specifies that the adhesive be applied with the flat side of the trowel to obtain a mechanical bond and proper coverage. Then the notched side of the trowel should be used to comb the adhesive to obtain an even setting bed.
Coverage. Beat in the tile with a beating block to obtain maximum contact of mastic to the back of the tile. Average contact should be no less than 80 percent, except in shower areas where 95 percent contact is required for a suitable installation.
Grouting. Wait 24 hours before grouting to allow evaporation from the mastic, lest discoloration or mottling of tile results. Make sure that you keep two-thirds of joint depth open for grout or you may experience subsequent cracking of the grout and/or discoloration.
ANSI A 136.1: What makes a good mastic?
It is under ANSI A136.1 that the standards are set. Because various degrees of water resistance are needed in ceramic tile installations (such as intermittent water-exposure situations), it is wise to contact the mastic manufacturer for guidance in extreme situations.A quality ceramic tile adhesive must have the appropriate shear strength, durability or stability in storage, flexibility, and water resistance. For approval under the standards, the adhesive must conform to tests for impact, staining and mold resistance, as well.
Adhesives are classified as Type I for walls and ceilings in commercial construction, light construction with dry or limited water exposure, or light construction with wet requirements.
Type II adhesives are designated for use in interior areas on walls and ceilings that have light construction with dry or limited water exposure.
The basic difference between Type I and Type II products boils down to their ability to resist water and the difference in shear strengths both wet and dry. For example, Type I must not have less than 50-pounds-per-square-inch (PSI) shear strength after immersion in water for seven days. A Type II adhesive is only required to have a shear strength of 20 PSI after the same period of immersion. (Immersion times are different for Type II.)
In addition, Type I may be used for ceramic floor tile installations but only in residential construction. Type II is used for walls and ceilings.
The Tile Council of America (TCA) has installation details for organic mastics as follows: F116-02, organic mastics over concrete subfloors; and F142-02, organic mastics over wood subfloors. TCA also has wall details W223-02 (solid backing) and W242-02 (gypsum board over metal studs), as well as details B413-02 (gypsum board) and B419-02 (coated glass mat) for bathtub walls.
Organic mastics have a history of evolution. The first mastics were solvent-based products that, even today, many consider the best. However the hazards, in terms of health effects and damage, resulted in the development of latex ceramic adhesives. These were originally made from Styrene Butadyne Rubber (SBR). These performed very well and many had shear strengths well in excess of 50 PSI. The latex used in these products was also used as admixes for thinsets and grouts.
Later came the acrylics, which are the main types in use today. Acrylics provided enhanced shear strength and were less susceptible to ultraviolet rays and discoloration -- especially in grout admixes.
A further development was urethane that doubled as a waterproofing agent and a tile-setting product. And another new entry claims to have reduced shrinkage, which is particularly important under large tile, and is said to be 25 percent lighter in weight.
When it comes to mastics, as is the case with the development of so many products in our industry, progress continues.
Looking for a reprint of this article?
From high-res PDFs to custom plaques, order your copy today!