Water: Nature's Best Friend but a Formidable Enemy to Tile Installations
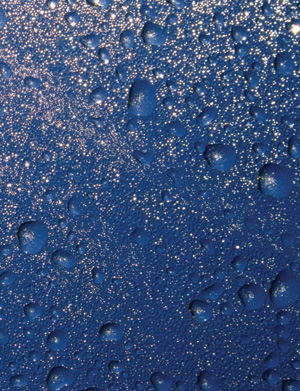

However, to get a better handle on the greatness of water, you'll have to consult an issue of National Geographic. Here at National Floor Trends, we care about floors. We want to buy them right, sell them to our customers and have them installed in problem-free fashion.
When ceramic tile walls or floors are the choice, many times the consumer falsely assumes that tile provides a waterproofing function. This is a very common misperception that typically remains unaddressed during the sales pitch by either seller or the buyer.
The result of this assumption is sometimes only realized after substantial damage has occurred to the customer's structure -- possibly months but, more often, years later. To add insult to injury, the warranty on the work usually has long since expired and, in many cases of water damage and resulting mold issues, there is no insurance coverage. The cost must be borne entirely by the unfortunate victim.
In all but the rarest of instances, such problems could have been prevented by either the sale or specification and proper installation of waterproofing. Even better, waterproofing represents an add-on sale for which many are very willing to pay when the risks to some installations are explained properly. Allow me to address some of the more prominent waterproofing facts and fantasies.

Tile and sealed grout don't offer protection
As I mentioned, the public's most widely held misconception is that a ceramic tile installation in some way affords protection from water damage. This erroneous belief is furthered when the grout has a sealer applied.An inert product, tile is unaffected by water in and of itself. Glazed tile is typically, but not always, impervious on its exposed surface. However, this protection does not extend beyond that exposed surface. In the case of wall tile used for extensively for tubs and showers, the water absorption of the tile body can be as great as 20 percent.
The grout used in installations is most often cement based. Grout is also unaffected by water, however, even good cement-based grouts can have an absorption rate of 7 to 15 percent. The more porous the grout, the greater its absorption. And it doesn't matter if it has been treated with a sealer, because such products are more of a cleaning aid than anything else. They slow the penetration of moisture and the accompanying soils, but they are not waterproofing products.
Some would say that using an epoxy would solve this whole grout problem and serve as a waterproofing. While there is no doubt that epoxy grout would substantially alter and nearly eliminate the absorption, it still does not constitute waterproofing. All it would take is a pinhole or small spec of exposed tile edge to render it useless in that application.
Lastly, from an installation perspective, many consumers and installers alike think that cement-based thinset mortars -- especially those that are latex or polymer modified -- provide some type of protection. While there are a few products on the market that will serve that function, it may surprise you to know that there are a fair amount of cement-based polymer thinsets that are actually water sensitive and will fail when exposed to moisture. This is even more an issue during the curing-and-coalescence stage where both are waiting final set, which could be weeks in some instances.

Effective waterproofing applications
When to use and not use waterproofing products? There are few areas where waterproofing, especially those providing some crack suppression, would not be beneficial. Among those not benefiting are damp concrete basements, which is another popular misconception. Tile-related membranes are made to keep water from passing through from the top into the structure, not to keep water in the structure from passing up through the floor.In the case of adhesive-applied membranes, failure is a good possibility when installed over wet slabs. If you must waterproof a slab subject to vapor or moisture issues, your options are limited. However, some breathable or vapor-tolerant membranes are available.
An excellent place to use waterproofing is basement showers. All shower floors should be waterproofed, including those on a basement slab. Unless waterproofed, all the shower water and its accompanying organic materials will migrate through the slab into the surrounding area.
Some very good applications for waterproofing are often overlooked. Aside from the traditional wet areas, such as tubs and showers, waterproofing makes real sense when used in many other areas. Ask your insurance agent how many hundreds of millions of dollars are paid each year for overflowing washing machines, leaky dishwashers and dripping refrigerator icemakers.
People with small children are often very receptive to providing some splash protection in their new bathroom floor. However, splash protection and flood protection are two separate uses of the products. For splash protection on the floor, one only needs to protect against the occasional puddle with no sealed penetrations. Flood protection is sealing all penetrations and turning the membrane up the wall to make the room capable of holding water, possibly hundreds of gallons. If waterproofing the floor for flooding is desired, don't forget that the water needs a place to go other than the adjoining hallway.
Kitchen countertops are another area sure to benefit from water protection. Regardless of how careful one can be, they most assuredly will end up wet. An area often overlooked is the underside of the cabinets where the dishwasher is located. That area is sure to receive moisture.
Tile is increasingly popular for deck applications, be they on-grade slabs (not a huge concern other than proper pitch), raised wood decks (a big concern) or roof decks (a huge concern). The requirements for above-grade decks are very exacting, and the limited space for this article does not allow me to explore them in depth. These types of projects are fraught with obstacles and should be left to only the very best available skilled labor.
Most typical failures occur due to railing penetrations, failure to allow for movement in the adjoining areas, lack of any type of counterflashing, inadequate drainage provisions, poor choice of substrate, and the inability of the supporting structure to remain stable. Claims for water damage in these types of installations can be staggering. Happily, tile can easily be used in these applications with problem-free performance provided that industry guidelines and manufacturer instructions are strictly followed.
Probably the most suitable areas for waterproofing are tubs, showers and steamrooms. Manufacturers have done an outstanding job of developing products to address these areas. Unfortunately, as more "floor coverers" take on the role previously handled by traditional tile setters, these areas have been plagued by a disproportionate increase in failures.
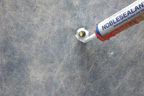
There are two very common problem areas in showers that are of equal concern. First is pre-pitch of the shower pan liner. This is typically a code requirement apparently unknown to many.
The following is an excerpt from the Universal Plumbing code, one of several code-publishing bodies: "All lining materials shall be pitched one-quarter (1/4) inch per foot (20.9 mm) to weep holes in the subdrain of a smooth and solidly formed sub-base."
Many mistakenly believe the shower floor itself serves as the as the pitch for water drainage when, in fact, the shower floor should be of equal thickness following the pitch of the liner below. The proper shower drain assembly actually is two drains, one at the top that we are accustomed to seeing and another at the bottom to allow for drainage of the floor on top of the shower pan liner.
If the liner is not pre-pitched, everything stays at the bottom of the shower under the floor. Over time, this will likely allow mold to develop. How soon or how bad depends entirely on use of the shower. Given the litigious nature of things these days, and varying tort laws coupled with lack of insurance coverage, you may want to examine the way you currently put in shower floors.
The second area of equal concern is the shower curb. Installers continue to put nails in the curb when using backerboard on curbs. Unfortunately, it will not be not very waterproof with 16 to 20 nails running through the top and inside of the curb. The other common omission is the failure to bring the waterproofing membrane down over the outside face of the curb (to fully protect the top from water migration) and extending the same protection up the sides of the doorway or jamb.
As you might expect, plumbing code has something to say about this too: "All such lining materials shall extend upward on the rough jambs of the shower opening to a point no less than three (3) inches (76 mm) above the top of the finished dam or threshold and shall extend outward over the top of the rough threshold and be turned over and fastened on the outside face of both the rough threshold and the jambs."
Once again, failure typically takes a few years to occur. If the installer does not know how to mud a shower curb or dam, there are many other options from which to choose. One, which is increasingly gaining favor, is to waterproof the surface to which the tile is to be applied. This eliminates the guessing and mere hope that the unit is waterproof.
If I were a distributor or retailer, I would make sure my salesforce was trained in the facts and fantasies of waterproofing and other membranes. If I were a salesperson, I would certainly be paying much more attention than in the past. The selling and installation of membranes not only increases the total dollar amount of the sale but also protects the customer's investment.
Waterproofing is one area -- offering profit and protection -- where both the seller and buyer can benefit.
Looking for a reprint of this article?
From high-res PDFs to custom plaques, order your copy today!