Causes and Prevention of Resilient Floor Discoloration

The new resilient floor was installed perfectly. The required maintenance program was explained to the customer in full detail. The customer, in turn, conscientiously performed preventative maintenance such as applying proper floor protectors to furniture, adding window coverings to guard against excess sunlight exposure, and laying walk-off mats near entrances for people to wipe their feet.
So where did that yellow stuff on the floor come from?
Despite the claims of some of the best flooring manufacturers, some stains on resilient flooring cannot be prevented under certain conditions. Therefore, gaining knowledge about the common causes of resilient discoloration is your best defense against being plagued by such problems. And sharing this information with the customer is the best way to prevent a complaint.
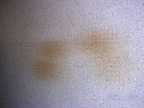
Why did the floor beneath the doormat turn yellow?
Rubber materials can cause a yellow stain on resilient floors. This is most often seen in areas where rubber-backed floor mats have been laid on the floor.However, this problem is not confined solely to rubber mats. Exposure to wheels on carts, automobile tires, some Durigan rubber backings on carpet, rubber floor rests, and even the base on those 3- to 4-foot-tall posts with retractable belts that are used for pedestrian control and queuing in banks and theaters can also contribute to the yellowing of floor coverings.
Antioxidants -- like butylated hydroxytoluene (BHT), among others -- are used in rubber formulations to keep them from prematurely aging and to prevent the rubber from getting brittle or cracking. When a product containing such compounds comes in contact with PVC floors, these chemicals will migrate into the surface of the vinyl material.
Some antioxidants are yellowish by nature. Others create the discoloration when they react with oxygen and light after migrating to the vinyl floor's surface. Essentially, the antioxidants in the rubber react with the plasticizers in the vinyl to allow chemical migration between the two materials.
This mechanism is related to the behavior of carbon atoms in the rubber compounds. Different rubber compounds can create varying degrees of staining. So, it is safe to say that this staining occurs because of a chemical reaction.
The bad news is that, once it occurs, the discoloration is permanent. The only way to repair it is to remove and replace the floor covering.
Do other types of mats also cause this staining?
Not all mats discolor resilient flooring. Consumers should be cautioned to obtain mats with frothed-foam PVC backings, jute-type backings or mats that the manufacturer claims are non-staining. Unbacked mats (woven mats or carpets without some type of non-slip backing) usually do not cause problems. However, they can be serious slip hazards.
Advise your clients to ask for non-staining mats. If they are unsure as to the mat's propensity to discolor, suggest that they test on a sample or on flooring located in a closet or other inconspicuous area.
In an effort to prevent this type of discoloration, flooring manufacturers can use expensive non-staining plasticizer in the manufacture of the floor. Polyurethane coatings also may help prevent staining, but there is no guarantee.
Other preventive measures include placement of protective Plexiglas or carpet mats under tires in auto showrooms, and applying felt instead of rubber feet on furniture. Today, you also see many forklift wheels with composite treads that are non-staining. This is particularly true in the electronics industry because electrostatic dissipative (ESD) vinyl tile typically is installed in their facilities all the way back to the loading docks.
It's worth noting that this type of staining from exposure to rubber can take place on many materials, even terrazzo and sealed concrete.
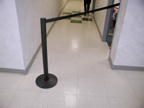
What else can permanently stain the floor from above?
Metal chair legs can leave rust stains on the surface of resilient flooring that can be very difficult to remove. This constitutes another good reason for applying proper floor protectors to the furniture.In addition, oil and grease attack the surface of resilient floor coverings and can cause a yellowing stain. Animal fats and cooking oils may soften rubber, which is why rubber flooring should not be installed in commercial kitchens.
Sun discoloration, even in structures with UV-coated windows, can still occur on certain types of flooring. This fact can afford you an opportunity for an add-on sale. Try selling some window treatments to go with that new floor and you'll be helping your customer to prevent this problem (as well as boosting the overall job ticket).
Asphalt tracking is an age-old problem, although many residential vinyl floorings are guaranteed against this malady thanks to the stain-resistant urethane formulations that were introduced around 1990. If a customer has a new driveway, or seals their driveway regularly, it would be wise to recommend a floor that will resist asphalt tracking.
On commercial jobs, pay careful attention to new parking lots or sealers, especially on new construction sites where there may be a lot of foot traffic on the floor before the initial maintenance is performed. Protection of a new floor during construction is critical for this reason and many others.
Other preventive measures include discouraging the purchase of very light-colored resilient floors, making sure the customer has a good mat program in place to clean the feet, and recommending the use of stain-resistant sealers or floor finishes. I was also told once that a latex-based asphalt sealer, in contrast to a coal-tar sealer, is more resistant to asphalt tracking.
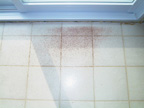
Stains emanating from beneath the floor
Resilient floors also are subject to staining from beneath in certain conditions. Mold or mildew can stain a floor that is installed over a damp substrate, especially when inferior patching compounds without mold and mildew inhibitors are used.Adhesive contamination from asphalt adhesive (the black stuff) can also create discolorations from below. Because the oils in the adhesive can attack vinyl, all adhesive residue must be properly treated before installing the new resilient floor. This entails either complete removal of the adhesive residue, or a thorough scraping down to just a transparent residue, followed by encapsulation with an approved patching compound or other surface-applied treatment.
Adhesive contamination from other adhesives can also occur due to plasticizer migration, which is a chemical reaction between the old adhesive, the new adhesive and the floor covering. It results in a permanent yellow stain.
To be absolutely safe, all old adhesives should be completely removed from the floor. Don't just patch over it! Failure to remove the existing adhesive also can cause it to soften from exposure to the water in the patching compound, or can result in a soft layer beneath the flooring that will lead to indentation. Again, your best bet is to remove all of the old adhesive.
Chemical adhesive removers, if not eliminated completely, can also stain the flooring from below. This is especially dangerous when the solution gets into the cracks in the concrete and works its way back upwards.
In conclusion, I wish to thank Tim Cole of Forbo, Tom Erisman and Ray Thompson of Armstrong, Jef Silfies and John Coppola of Tarkett, and Fred Roche and Wally Ruttgeiizer of Parterre flooring for contributing expert information and/or photographs in support of this article.
Looking for a reprint of this article?
From high-res PDFs to custom plaques, order your copy today!