Tile Grout: Friend or Foe?
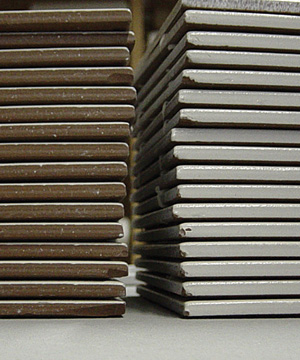
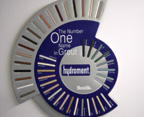
"Had our house tiled a year and a half ago, and about two months after the job was done, started to notice the sealer ‘wearing away.' Upon closer look, I noticed the grout was powdery, and coming out. What, in your opinion, could cause the grout to become powdery in only two months?
"It's sad, and very disappointing, to look at the floor today, 1 1/2 years later. Large areas of grout have come up all throughout the house, and the nearly new floor we paid $5,000 for looks so bad. The original contractor will not help, and has tried to blame the problem on our dogs."
Does this sound like a repeat or referral customer? Or will she tell everyone she knows that she will never buy tile again because of her bad experience? While installation is my specialty, I have handled sales all my life as well. During the course of my years as a retailer and contractor, I can say that, after having sold millions of dollars worth of installed products, the number of complaints we've received relative to installed tile and grout shading can be counted on two hands. In dollar value, the loss was quite minimal. In goodwill generated by lack of complaints, the value was priceless.
While this article primarily addresses product and installation, the first step in making customers and end users happy is the proper presentation of the product. Installed grout, with rare exception, will not perfectly match the sample. The reasons relative to the installation process are numerous. Those from the manufacturing side are few and far between.
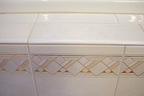
Several manufacturers also offer liquid latex additives in lieu of (or in addition to) dry polymer formulations. The chip sets typically employ a latex additive, if available. When it comes to printed grout cards, the limitations of ink and paper relative to pigment, sand and cement should be apparent to the professional.
To the consumer, however, this is not the case; they expect it to look exactly like the sample. If you do not inform the consumer of these limitations during the sales process, you can be assured of receiving numerous complaints.
After the selection and sale, there are numerous other items that can affect shading before the installer ever opens the bag of grout. This list includes:
- Overglazed edges on the tile. This is a common practice, intentionally done by some manufacturers, where the exposed edge is used as trim.
- Glaze on self-spacing lugs in wall tile.
- Porosity of the tile body. Impervious tile will prevent the rapid absorption of water vs. a wall tile, which will rapidly absorb it.
- Dye lots. Manufacturers use multiple plant locations in the processing of product and blend numerous different colors during the normal course of production. Always check the dye lot. On larger jobs, you should blend bags while still dry to achieve the greatest color consistency.
- Use of clean buckets and good, potable water. The need for clean buckets should be self-explanatory. Clean water can be hard to come by on construction sites with new wells. High amounts of chemicals, good or bad, can cause problems.
- The house should be fully acclimated prior to tile and grout installation. Temporary heat causes permanent problems.
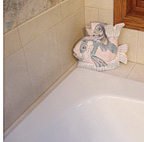
For some reason, the low man on the totem pole always seems to get the job of grouting. It is his job to provide the desired aesthetics. His installation and cleaning methods will also determine whether the end user faces a lifetime of easy care or misery.
Consider the following as well:
- If a light-colored grout is to be used, it's best that the tile is installed with white thinset mortar.
- The joints should be clean and free of debris, including the construction dust typical of most job sites.
- The thinset in the joints should be of uniform thickness. Troweling parallel to the tile and positioning your next piece directly next to the previously installed tile and then sliding in for coverage and position makes this much simpler to achieve.
- The tile should be wiped down with a damp mop or sponge. Moistening the surface prior to installation goes a long way towards easier cleanup. Otherwise, the tile surface's first exposure to moisture will be the moisture in the pigmented grout. That's not a good idea.
- Tile setters do not own fans. Cement must cure at it's own pace. Fans cause rapid loss of water, which results in light and weak grout.
- Use of latex or polymer in the thinset mortar mandates use of latex/polymer grout.
- All movement joints and inside corners should be caulked before grouting.
- Use a low-speed mixing drill to mix the grout. Too much air in the mix results in weak grout. If you're using a 3/8-inch drill, you are mixing too fast. Depending on the recommendations of the grout manufacturer, 100 to 300 RPM is an acceptable range for mixing. Be aware, however, that recommendations vary between product suppliers.
There is no corrective measure for poorly installed grout short of removal (although some may chose to argue and attempt to mask the shortcomings). Excessive use of water in both mixing and cleanup leads the way as the top reason for complaints on grout, period. A little effort towards educating the customer, and some care by the installer, can result in years of complaint-free tile installations -- the most profitable kind.
Looking for a reprint of this article?
From high-res PDFs to custom plaques, order your copy today!