Ask the Expert: More Answers to Your Resilient Inquiries
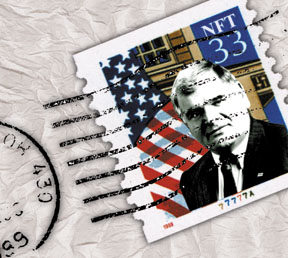
My articles frequently elicit reader questions about resilient floor coverings and their installation. This month, I’ve plucked a dozen such inquiries from my files. By sharing them with you now, I hope you’ll gain some practical insights that can help you when, and if, you come across similar situations during the course of running your business.
Q: Why is the heat welding of linoleum so different from the welding of sheet vinyl?
A: Where welding of PVC (vinyl) materials are concerned, a thermo-fusion process must occur. This fusion takes place partially in the weld rod and partially in the flooring material itself. In the case of linoleum, the thermo-bond takes place entirely in the rod. For this reason, heat welds are stronger in vinyl products.
Q: What are the causes of underlayment joint show-through in wood underlayment panels?
A: There are several causes of underlayment joint show-through. Perhaps the most common is improper acclimation of the underlayment to the surrounding environment in which it will be installed. There should be no more than a 3% difference between the moisture content of the subfloor and the underlayment. Another common cause is improper fastening of the panel edges. Most underlayment manufacturers require a specific fastener spacing procedure, including a recommended distance from the panel edge and correct length and size of fastener.
Q: What causes failures of seam-sealed floors?
A: Failure of sealed seams can occur for a variety of reasons. Sometimes, it’s due to the installer’s inability to get the seam sealer down into the seam. The fin of the sealer applicator bottle must be inserted into the seam to obtain a complete top-to-bottom seal. Other times, flooring adhesive contaminates the seam edges. For the sealer to perform adequately, the seam must be completely free of any type of contamination. Finally, failure can occur when there’s a void in the seam that’s too large for the sealer to bridge. The seam must be cut so that both edges of the flooring material achieve a net fit.
Q: I’ve experienced a bond failure in a floor installed over a substrate that was asbestos abated. Can you identify possible causes for this failure?
A: In cases of asbestos abatement, an adhesive remover is often used. Adhesive removers cannot distinguish between old and new adhesives. So, if the product isn’t cleaned up properly after the old adhesive is removed, it will eventually attack any new adhesive that comes in contact with it. Another possible cause of a failure relates to the use of an encapsulant, which is a coating used over the surface of the substrate. These coatings have been known to cause bond failures.
Q: Can you elaborate on why manufacturers do not recommend installation of new flooring material over more than one layer of existing material?
A: The main reason relates to indentation of the new material. With each layer of material, the floor’s static load capability diminishes. Also, there is no way to know how well the existing layers of flooring are bonded to each other. Experiencing a failure of the new floor is an unwise way to find out.
Q: One of our vinyl composition tile (VCT) installations failed due to what appeared to be a moisture problem on a suspended slab. But when we checked the slab, the calcium chloride vapor emissions tests the were within the levels recommended by the VCT manufacturer. What do you think caused the problem?
A: If the suspended slab was not heated from beneath, and the slab temperature, ambient room temperature and humidity were just right, the slab could have gone through dew point. Dew point refers to the point where the moisture condenses on the surface of the slab. This condition is often mistaken for a moisture problem. The only ways to avoid this situation is to either insulate the underside of the slab or heat the area beneath it. With new construction, dewpoint is a common problem — especially on jobs that have temporary heat — and it’s often misconstrued as a moisture problem.
Q: When applying an adhesive on a warm day over a dry and porous substrate, the adhesive starts to dry before the entire area is spread. What can I do to extend the drying time of the adhesive?
A: Basically, you have two options. The first is to use a sprayer to lay a fine water mist over the surface of the substrate. Though this will slow the absorbency of the substrate, care must be taken not to over-dampen it. The second option is to spray a fine mist in the air over the spread adhesive. This will slow the evaporation of the water in the adhesive and also raise the ambient humidity, which will slow the adhesive’s drying time.
Q: What are the causes of wood underlayment panel joint show through?
A: There are several. The first cause is failure to acclimate the panels. The moisture content of the underlayment panels must be within 3% of the subfloor panels. Another reason can be improper fastening of the panel edges, particularly when the fasteners are set too far apart or too far from the panel joints. A third reason could be the use of improper fasteners to anchor the panel edges. Examples include fasteners that are too long, not the type specified by the underlayment manufacturer, or those driven too deep into the underlayment panel. Finally, the problem may be due to improper preparation of the panel joints, especially when the patching compound used does not have sufficient compressive strength. This can occur from using an incorrect patching compound or even from over-watering the correct type of compound.
Q: It seems that more installations have an overspray of paint on the surface of the substrate. Does the paint residue have to be removed?
A: Yes, most paint overspray is of the latex variety. When a latex adhesive is applied over the residue of latex paint, the latex emulsifiers in the adhesive will soften the paint and break its bond to the surface of the substrate. This, of course, is just one more situation that will cause an installation failure.
Q: What are your thoughts about the relative merits of trowelable underlayment compounds vs. self-leveling underlayments?
A: It depends on one’s expectations. Trowelable underlayment is labor intensive and slower to apply. It also requires sanding, usually a second coat, and then a final sanding before the installation. However, trowelable materials are less expensive. Self-leveling underlayment materials are faster to apply (about eight times faster than hand troweling), and they require little, if any, touch-up to the finished surface. But the cost of self-leveling materials is comparatively greater. I think that if your primary aim is to produce a great-looking installation, then the self-leveler is the way to go.
Q: Are you aware of any super fast-setting patching compounds for concrete slabs?
A: Some of the new magnesium oxide-based patching compounds used by the concrete industry will set to 4,000 psi within one hour but, at this time, I am not sure how compatible they are with flooring adhesives. Some compatibility testing is currently underway.
Q: What would cause a concrete slab to be acidic rather than alkaline?
A: A concrete slab is generally at a pH level in the range of 12 to 13. Only a couple of variables could cause a slab to be acidic. A broken sewer line beneath the slab or methane gas diffusing up through the slab could be the culprit. The chemical reaction between methane gas and concrete will create sulfuric acid. Though this type of a condition is rare, it can occur. A good vapor barrier placed beneath the slab might prevent an acidic slab situation from developing.
Ray welcomes your questions and comments about this or any other article he’s written. You can contact him in care of NFT or e-mail him at www.rayt-fci@cleelum.com.
Looking for a reprint of this article?
From high-res PDFs to custom plaques, order your copy today!