Urethane, You're a Pain. Prepping a sub-floor when epoxy jams the joints
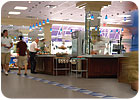
Food
for thought: This commercial resilient flooring from Johnsonite looks perfect.
But remember, to avoid problems down the road it is the installer's
responsibility to make certain the sub-floor has been properly prepped and
inspected.
All too often I come across something beneath a resilient floor that could spell trouble: Saw cuts filled with an epoxy-type of joint filler. The product used is a two-component urethane mixed and then inserted into the saw cut joint. It turns out the manufacturer of the joint filler recommends that its product be used to fill the saw cut joints whether indoors or out. But they do not make any recommendation for their product if it is to be used beneath an applied flooring material. That’s where the trouble can come.
The architectural community has been specifying the urethane filler for walking areas of bare concrete and it has worked out well. But they also specify it for all situations, including under resilient products.
In my travels I have encountered it a number of times. For example I once saw urethane filler employed beneath VCT tile in a supermarket Wherever there was a joint, the tile was cracked. This, no doubt, was the result of shopping-carts, fork lifts and other rolling traffic. In this case the architect demanded that the flooring contractor replace the affected tile. He did, and the same thing occurred a second time.
Under sheet flooring you do not get the same cracking. Instead, you get is a bulging of the saw cut that shows through the material. Once the joint opens up, it is obvious the bulging is caused by the filler.
Flooring contractors must identify the problem before the flooring goes down. Once the floor is installed the flooring contractor, by default, becomes responsible for the problem. So if you spot this type of situation, what’s next? It is costly and labor intensive, but it is solvable.
Steps to handle a joint if urethane has been inserted
1) REMOVE The urethane filler must be entirely removed. This usually requires chasing (recutting) the saw cut. The reason is, cementitious patching compound will not stick very well to a urethane residue. By chasing the joint it opens up the pores of the concrete allowing for a better mechanical bond of the filler. These saw cuts are generally 1" deep and require a thorough and complete cleaning.
2) REPLACE Once cleaned out the saw cut is ready to be filled. The filler must be a high compressive strength (exceeding 4,000 psi). In order to achieve this high compressive strength the patching compound must be mixed stiff with a minimal amount of water. Manufacturers will have the proper powder to water ratio to follow to achieve the highest compressive strength.
3) POWER MIX Once the powder is placed into the water I prefer to power mix with a drill. The power mixing will break the surface tension of the water and allow the mix to be thinner than if hand mixed.
4) DAMPEN JOINT Just before application of the filler I will dampen the joint. This will make the application of the filler easier. And be thorough: You need to get the filler to the complete depth of the saw cut. This way, you’ll help prevent future joint show-through concerns. You will find it more difficult to work the filler down into the total depth of the joint, but the long term results for the effort will pay off.
It is best to take a pro-active approach and review the architectural specifications prior to bidding on the job. Many of these specifications can be handled prior to the application of the urethane being installed, because once it is installed it is difficult to correct.
Looking for a reprint of this article?
From high-res PDFs to custom plaques, order your copy today!