Which test is best for concrete answers?
Installers frequently
ask me which method of moisture testing is the most reliable. I also encounter installers who wonder: Is there a correlation between Calcium
Chloride and RH Probe testing? These are important concerns because moisture
issues continue to a big problem for installers. To look at the answers, let’s
first examine the affect of water on a concrete slab.
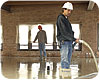
Installers frequently ask me which method of moisture testing is the most reliable. I also encounter installers who wonder: Is there a correlation between Calcium Chloride and RH Probe testing? These are important concerns because moisture issues continue to a big problem for installers. To look at the answers, let’s first examine the affect of water on a concrete slab.
Water is a complicated and vital element of a concrete slab. Too much water and the slab will not properly receive moisture sensitive flooring material. This is because water used in a concrete slab dictates its compressive strength, permeability and the amount of drying time required. Water is also a “non-compressible” liquid. That means excessive water displaces the other solid compounds in concrete. Once the slab dries, the resulting voids and capillaries enable future moisture to migrate in and out of the slab. Water is also it heaviest when it is in liquid form. It becomes lighter as a solid (ice), and lighter still as a gas (steam). That means water thickens in colder conditions and thins as it is warmed. The temperature at the job site immediately after a slab is poured plays a huge part in the voids and capillaries.
In liquid form, water seeks a colder/damper environment (the bottom of the slab), then the liquid turns into a vapor (an expansion of the water molecule 1700 times) it migrates to the warmer, drier side of the slab. The loss of the water vapor is how the slab dries.
Concrete requires very little water to get it to set. The extra water is used to assure the placement of the concrete. ASTM F-710 “Standard Practice for Preparing Concrete Floors to Receive Resilient Flooring”, states; “moderate to moderately low water-cement ratios (0.40 to 0.45) can be used to produce floor slabs that can easily be placed, finished, and dried, and which will have acceptable permeability to moisture. Floor slabs with water-cement ratios above 0.60 take an exceedingly long time to dry and cause adhesives or floor coverings, or both, to fail due to high moisture permeability”. The recommendations by the flooring Industry is not to exceed a water cement ratio of 0.50.
To assure that you’re in compliance with the industry standard, you must test the slabs moisture level. The calcium chloride test measures the Moisture Vapor Emissions Rate (MVER) at the top 1/2 to 3.4” of the surface of the concrete. Of course the test is meaningful only when done right. To assure accuracy keep these tips in mind:
• Temperature: Test conditions should be 75°F ± 10°F (23.9°C. ± 5.5°C). Maintain these conditions 48 hours prior to, and during testing.
• Relative humidity: Test conditions should be 50% ± 10 % relative humidity. Maintain these conditions 48 hours prior to, and during testing.
• Multiple tests: Three tests for the first 1,000 square feet and one for every 1,000 square feet thereafter.
• Clean slab: Removal any residues on the slab surface, even the residue in the pours of the concrete. (Otherwise they will affect the moisture vapor drive.)
• Seal the test dome: The plastic dome must be sealed and airtight to prevent ambient humidity from influencing the test results.
• Weighting the Petri dish: This needs to be done one-hour before and one-hour after the testing. The weight needs to be calculated within 0.1 grams.
• Timing: It is recommended that the elapsed time of the test be 60 to 72 hours. Anything less and you invite an abnormally low reading (false positives); anything more and you risk abnormally high reading (false negatives).
• Consolidation of the concrete surface: Hard trowel finishes slow the migration of moisture vapor, but there are no known simple methods of calculating its effect.
• Conditioning of the slab: The temperature of the slab must be up to service temperature. Failure to do so will drive the moisture to the bottom of the slab yielding false positives in test results. Determining if the slab is in equilibration is the missing part of true calcium chloride testing accuracy.
The relative humidity (RH) probe testing helps eliminate a lot of the guess work from moisture testing. In involves drilling a hole down to 40-percent of the depth of the slab. (That is where the apex of the drying curve intersects with the equilibrium line.) To assure accuracy, however, the following conditions must be met:
• Concrete slabs must be at service temperature at least 48 hours prior to the testing.
• Number of tests needed is the same as calcium chloride: three tests for the first 1,000 square feet and one for every 1,000 square feet thereafter
• Depth of the probes shall be 40% on slabs drying from the top only and 20% for slabs drying from both sides.
• The probe must be calibrated for accuracy at least once a year
• The probes must be allowed to acclimate and checked for drift less than 1% relative humidity over a 5 minute period.
• Elapsed time for the test is 48 hours, (I believe this will be shortened).
To answer the question “Which test should I use?” the trend among resilient flooring manufacturers is to use RH probes, some exclusively, because it is more scientific. The calcium chloride testing is still going to be used, especially for gauging the effectiveness of moisture mitigation treatments. Still, the potential for erroneous testing in the field (by both professional testing firms and flooring contractors) means the calcium chloride testing will continue to fall out of favor.
As for the correlation between the two types of tests, there are none. There are some similarities. Because the outflow of moisture movement is dependant on the consolidation of the concrete surface, that is all.
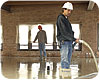
Installers frequently ask me which method of moisture testing is the most reliable. I also encounter installers who wonder: Is there a correlation between Calcium Chloride and RH Probe testing? These are important concerns because moisture issues continue to a big problem for installers. To look at the answers, let’s first examine the affect of water on a concrete slab.
Water is a complicated and vital element of a concrete slab. Too much water and the slab will not properly receive moisture sensitive flooring material. This is because water used in a concrete slab dictates its compressive strength, permeability and the amount of drying time required. Water is also a “non-compressible” liquid. That means excessive water displaces the other solid compounds in concrete. Once the slab dries, the resulting voids and capillaries enable future moisture to migrate in and out of the slab. Water is also it heaviest when it is in liquid form. It becomes lighter as a solid (ice), and lighter still as a gas (steam). That means water thickens in colder conditions and thins as it is warmed. The temperature at the job site immediately after a slab is poured plays a huge part in the voids and capillaries.
In liquid form, water seeks a colder/damper environment (the bottom of the slab), then the liquid turns into a vapor (an expansion of the water molecule 1700 times) it migrates to the warmer, drier side of the slab. The loss of the water vapor is how the slab dries.
Concrete requires very little water to get it to set. The extra water is used to assure the placement of the concrete. ASTM F-710 “Standard Practice for Preparing Concrete Floors to Receive Resilient Flooring”, states; “moderate to moderately low water-cement ratios (0.40 to 0.45) can be used to produce floor slabs that can easily be placed, finished, and dried, and which will have acceptable permeability to moisture. Floor slabs with water-cement ratios above 0.60 take an exceedingly long time to dry and cause adhesives or floor coverings, or both, to fail due to high moisture permeability”. The recommendations by the flooring Industry is not to exceed a water cement ratio of 0.50.
To assure that you’re in compliance with the industry standard, you must test the slabs moisture level. The calcium chloride test measures the Moisture Vapor Emissions Rate (MVER) at the top 1/2 to 3.4” of the surface of the concrete. Of course the test is meaningful only when done right. To assure accuracy keep these tips in mind:
• Temperature: Test conditions should be 75°F ± 10°F (23.9°C. ± 5.5°C). Maintain these conditions 48 hours prior to, and during testing.
• Relative humidity: Test conditions should be 50% ± 10 % relative humidity. Maintain these conditions 48 hours prior to, and during testing.
• Multiple tests: Three tests for the first 1,000 square feet and one for every 1,000 square feet thereafter.
• Clean slab: Removal any residues on the slab surface, even the residue in the pours of the concrete. (Otherwise they will affect the moisture vapor drive.)
• Seal the test dome: The plastic dome must be sealed and airtight to prevent ambient humidity from influencing the test results.
• Weighting the Petri dish: This needs to be done one-hour before and one-hour after the testing. The weight needs to be calculated within 0.1 grams.
• Timing: It is recommended that the elapsed time of the test be 60 to 72 hours. Anything less and you invite an abnormally low reading (false positives); anything more and you risk abnormally high reading (false negatives).
• Consolidation of the concrete surface: Hard trowel finishes slow the migration of moisture vapor, but there are no known simple methods of calculating its effect.
• Conditioning of the slab: The temperature of the slab must be up to service temperature. Failure to do so will drive the moisture to the bottom of the slab yielding false positives in test results. Determining if the slab is in equilibration is the missing part of true calcium chloride testing accuracy.
The relative humidity (RH) probe testing helps eliminate a lot of the guess work from moisture testing. In involves drilling a hole down to 40-percent of the depth of the slab. (That is where the apex of the drying curve intersects with the equilibrium line.) To assure accuracy, however, the following conditions must be met:
• Concrete slabs must be at service temperature at least 48 hours prior to the testing.
• Number of tests needed is the same as calcium chloride: three tests for the first 1,000 square feet and one for every 1,000 square feet thereafter
• Depth of the probes shall be 40% on slabs drying from the top only and 20% for slabs drying from both sides.
• The probe must be calibrated for accuracy at least once a year
• The probes must be allowed to acclimate and checked for drift less than 1% relative humidity over a 5 minute period.
• Elapsed time for the test is 48 hours, (I believe this will be shortened).
To answer the question “Which test should I use?” the trend among resilient flooring manufacturers is to use RH probes, some exclusively, because it is more scientific. The calcium chloride testing is still going to be used, especially for gauging the effectiveness of moisture mitigation treatments. Still, the potential for erroneous testing in the field (by both professional testing firms and flooring contractors) means the calcium chloride testing will continue to fall out of favor.
As for the correlation between the two types of tests, there are none. There are some similarities. Because the outflow of moisture movement is dependant on the consolidation of the concrete surface, that is all.
Looking for a reprint of this article?
From high-res PDFs to custom plaques, order your copy today!