Revitalized Concrete Flooring Streamlines Building Maintenance
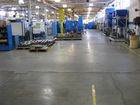
Pictured is the floor of the Cone Drive facility in Traverse City, Mich. before treatment.
When looking to repair and revitalize the aging concrete floors throughout its 150,000+ square foot facility in Traverse City, Mich., Cone Drive specifically aimed for a finished floor that would not only look great but also – most importantly for the bottom line – be easy to maintain.
Over the years the floors at Cone Drive, the world leader in double enveloping worm gearing, had been coated and recoated with epoxy many times but were difficult and costly to maintain because the coatings invariably wore off quickly.
“The main reason we decided to redo the floors was that we didn’t want to go through the process any longer of removing the old epoxy and applying a new coat,” said Jordan Lewis, the operational improvement manager in the manufacturing and engineering group at Cone Drive.
To achieve the goals of visual appeal, durability, and low cost easy maintenance, the company turned to a concrete floor treatment that transformed the aging, worn floor into a shiny, slip resistant surface. The treatment, FGS PermaShine (a proprietary polishing and hardening/densifying system by L&M Construction Chemicals, www.lmcc.com), was applied to about 65,000 square feet of heavily trafficked areas of the plant, in stages over the past few years.
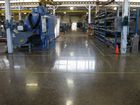
The next two images show the Cone Drive facility floor after treatment from L&M Construction Chemicals.
“Since we started the revitalization, we have had the opportunity to see how well the floor holds up and are very satisfied with the finishing. Plus we get a lot of positive comments,” he noted.
In many locations of the plant, it was necessary to grind away up to a quarter inch of old epoxy and other lumps and bumps before polishing the floor and applying the hardener/densifier.
The dust-free, waterless, dry grind polish process utilizes a series of progressively finer diamond-impregnated disks in a grinding machine for the smoothing and polishing. The number of grinding passes is determined by the specified degree of shine. The grinder uses an extremely efficient HEPA filter and vacuum air purification technology for collecting any generated dust, minimizing the need for cleanup of dust after the work is complete.
The proprietary chemical hardener/densifier is a vital and essential part of the treatment, first increasing the density of the surface, in the first application, and then reacting with the near surface wear zone (the top 1/8 of an inch) in the second application. The applications, which take place before the final pass of the grinding machine, produce a concrete surface that is far more abrasion-resistant and far less absorptive than the original concrete surface, according to L&M Construction Chemicals.
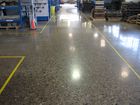
The hardener/densifier process results in a polished concrete floor that will require minimal upkeep over the life of the building, the company noted, This can save owners considerably on the cost of maintenance, short and long term. In addition, the treated finished floors will resist dusting and micro-pitting for years.
Both mechanically and chemically, the dry polish, hardener/densifier process is designed to limit exposure to hazardous components and pollution. In fact, a dry polished concrete floor can contribute points toward up to five different LEED credits under various categories, including Low Emitting Materials, Materials and Resources, and Energy and Atmosphere.
“It is great stuff - we work with oils and coolants which, if spilled, wipe right up. They don’t soak in,” said Lewis. “For maintenance, we sweep the floor and go over it with a scrubber using a mild conditioner. That’s all we have to do. We don’t wax or coat the floor at all, yet it really looks like terrazzo. It is beautiful.”
And there’s an additional - unexpected – benefit. “The light reflectivity of the new floor is so much higher that we now have a much brighter plant.”
Additionally, since concrete absorbs heat during the day and radiates that heat out at night, the delay in the cycle can help lower HVAC energy costs. Since the dry polish concrete process requires only a single application and generally costs 25 to 50 cents per square foot yearly to maintain, it can also lead to a significant reduction in maintenance costs.
Floors finished with the FGS PermaShine system comply with ADA and OSHA requirements for interior floor surfaces. They also meet the National Floor Safety Institute standards for certification as a “high traction” floor, retaining the non-slip qualities when wet. The whole process generates no odor and does not require clearing out the work area beyond the floor surface, with no need to remove items from shelves in or near the work area.
As Cone Drive discovered, even in occupied spaces under renovation, almost any structurally sound finished or unfinished concrete floor can be smoothed, dry polished and hardened and densified, with minimal disruption of business operations. The whole process, start-to-finish, can fit into an 8 to 10 hour work schedule.
Looking for a reprint of this article?
From high-res PDFs to custom plaques, order your copy today!