Sound Investment: Underlayment Can Boost Acoustical Performance
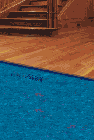
QuietWalk underlayment from MP Global Products.
Contractors, architects, distributors and retailers doing business with owners of new and renovating rental units and condos should recommend or specify acoustical floor underlayment for under new finished floors that meets or exceeds local building department acoustical standards. If the standards are not met, the building owner may pay the price when a tenant complains about noise or, even worse, sues over the noise.
Under wood, laminate, or ceramic tile flooring, the right floor underlayment can noticeably improve acoustic properties, quieting impact sound, dampening ambient sound and inhibiting sound from travelling into the room below.
Typically, specifying code approved underlayment falls within the responsibilities of the architect. However, sometimes plans can be ambiguous, specifying only compliance with a particular section of the code, rather than an approved product. Or the architect may select a product that does not meet local building code specifications for sound attenuation.
It is a good idea, before construction or renovation gets to the floor, for the specifier to select or the retailer to advise appropriate underlayment that conforms to local acoustics code or better. Unless there is clear documentation for the acoustical properties, the owner may hear about shortcomings after completion of the building or even after occupancy.
“The builder and/or the owner are often held responsible even though the applicable specifications or lack thereof are the architect’s responsibility because it is extremely difficult, after the fact, to figure out whether the level of footfall noise that people are complaining about is due to the design or the construction,” noted Charles Salter, president of acoustical consultants Charles M. Salter Associates, in San Francisco. Salter, an acoustical engineer, has been an expert witness for more than 100 condominium lawsuits.
“From an owner’s point of view, it pays to be educated about applicable standards and make sure the flooring contractor uses products that have been laboratory tested, because the code is predicated on laboratory tests of assemblies, not individual products,” Salter added.
In every locale, there are code requirements for floor underlayment to meet specific fire ratings. However, only some locales have code requirements that necessitate the use of cushioned underlayment to mitigate foot fall noise and muffle sounds of voices and music. These code requirements vary by the type of project and may also vary by state or even county within a state.
Furthermore, just meeting minimum code requirements is probably not good enough for for-sale housing. Minimum acoustical codes were written some years ago, initially promulgated by HUD low-cost housing, and those same standards are in the Uniform Building Code and the International Building Code.
“Buyers and renters in expensive dwelling units would have expectations that go way past code,” Salter pointed out. “It is not a good argument that the building meets code because in the luxury and even middle income housing market, there is an implicit as well as explicit expectation that the dwelling unit goes beyond minimum code requirements.
Typically, when there are minimum acoustical standards, the drawings should call out acoustical features such as the cushioned underlayment. Frequently, the building department requires lab reports that show the product has been tested in a construction of the same type.
If a project is examined because of possible substandard acoustical insulation in one location, the plaintiff’s attorney will likely assume that deficiency is pervasive and put in a multimillion dollar claim for acoustical defect throughout the project, Salter said.
The builder and owner now must be on the defense to show that the defect is only in one or a few locations, not throughout the project, which can become extraordinarily complicated and expensive. “It is important to pick the right products, have them installed correctly and inspected properly at the time of construction or renovation to avoid the downside risk of opening up floors and walls to look for inconsistent construction that could explain why people are bitterly complaining about acoustical problems,” Salter explained.
It is always best when a project uses a product that carries independent, third party test results. First party certification is essentially self-certification by the manufacturer. Second-party certification usually involves assessment by a trade organization. Third-party certification is conducted by an independent, unbiased laboratory and is typically the most rigorous. Manufacturers who go to the effort and expense of third-party certification likely make that information readily available on their websites and in product literature.
When evaluating floor underlayment, the building departments, acoustical consultants and others often rely on tests to define the performance of a floor/ceiling assembly - how well they insulate against noise created by impact and by airborne vibration.
There are two tests performed in a controlled laboratory environment recognized by the International Building Code for sound that travels from one living area down to another, including in a multi-family residential complex: Impact Insulation Class (IIC) and Sound Transmission Class (STC). IIC tests the ability to block impact sound by measuring the resistance to transmission of impact noise or structure-borne noise. STC evaluates the ability of a specific construction assembly (e.g. floor, window, door) to reduce airborne sounds, such as voices, stereo systems, and TV. The higher the number, the higher the resistance.
An IIC rating of 50 from a particular floor/ceiling assembly satisfies the requirements of the Uniform Building Code. Even though it satisfies the UBC, it does not necessarily satisfy tenants, who--with that level of insulation in the floor/ceiling assembly--are likely to still notice and complain about footfall noise. So specifying products that, put together as a floor-ceiling assembly, can achieve a higher score, like 57 or 58, would lessen chances of complaints.
Field tests (FIIC) for the same properties may be conducted in an actual building, as well, after the floor installation is completed. The UBC calls for a rating of at least 45 in this test. Underlayment is available that, in certified field sound tests performed at an installation over a standard concrete sub-floor, receive scores as 60, buffeting sound transmission that much more effectively.
FIIC is generally called for to address one of three conditions, Salter said. The building department may have approved the project but there was no acoustical design completed, and before occupancy can occur, the building department requires field testing to show the building complies with the acoustic code requirements.
Another condition: Though the building was designed properly and has a building permit, during the course of construction there were many product substitutions and the building department is concerned that what was called for in the design documents was not implemented, Salter said.
A third condition, and the least welcome, is complaints or a lawsuit involving acoustics, where the testing is done to determine if the building was built correctly according to code.
A few sound-attenuating underlayment products that are clearly manufactured to fulfill environmental interests and are made partially or substantially from recycled materials can also satisfy sustainability criteria. That’s a plus for any construction or renovation promoted as green. While it can be difficult for a contractor to determine if underlayment is green, selection of products that carry third-party certification validates the material and, in some cases, the manufacturing process as well.
Using products that are third-party certified will also help earn Leadership in Energy and Environmental Design (LEED) credits in several categories. Building products can earn credits in one or more of the six categories for new construction or renovation.
Sustainable sound attenuating floor underlayment may contribute to earning credit in Material and Resources; earning one credit if the project can satisfy a minimal 10 percent composition of recycled materials, or up to two credits if the project can validate minimal 20 percent composition of recycled materials. The same product can also meet LEED standards for low emissions and therefore contribute in the category of Indoor Environmental Quality.
Other benefits
·Can help smooth out minor imperfections in the subfloor, enabling the top finish surface to lay flat.·Added cushioning underfoot lessens the strain of each footfall on knee and hip joints, resulting in more comfortable walking (a good selling point in a senior community sales brochure).
·Improves thermal insulation, helping keep the floors warm in cold weather and cool in warm weather. The higher the R-value of the floor system, the lower the rate of heat loss in winter and loss of conditioned air in summer. Underlayment is available that can add .50 to the floor system.
·Under laminate or wood floors, some underlayment can help protect the flooring material from subfloor moisture that can ruin the finished floor.
·Under ceramic tile, helps avoid lateral crack suppression.
·Under any finished floor, firm underlayment can provide proper support to prevent premature wear and tear.
Looking for a reprint of this article?
From high-res PDFs to custom plaques, order your copy today!