Adhesive Application - To Trowel, Roll or Spray
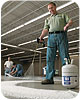
When using a spray adhesive, such as Azrock by Tarkett’s SpraySmart product (pictured), be sure to keep the spray smooth, with special attention paid to spray overlaps. Photo courtesy of Tarkett.
The backings of commercial resilient materials have changed over the past few years. Today, the majority of backings are no longer mineral felt. They are now vinyl-backed, either homogeneous or heterogeneous. Vinyl-backed materials (due to plasticizers) cannot use the same type adhesive as felt-backed materials.
It is imperative you use the correct adhesive/flooring product combination. Using the wrong adhesive can lead to job failure and more problems. The changes in backings have also brought on changes in adhesives – from a premium latex adhesive to a type of acrylic adhesive.
Acrylic adhesives created a lot of changes in the application and open time. Vinyl-backed sheet vinyl has no capability to diffuse the moisture in the adhesive, so any moisture left would have to be absorbed into the substrate. The problem begins when the substrate has little or no wicking capability. The industry, needing to find a solution for this problem, gravitated to a pressure sensitive or dry-to-touch adhesive.
Pressure sensitive or dry-to-touch adhesives are not without concern. The pressure sensitive adhesives are either soft- or hard-setting. The softer setting adhesives tend to be prone to indentations and adhesive tracking.
The harder setting adhesives tend to telegraph any adhesive irregularities through the material. What this means is the installer must place a smooth even trowel coat on the substrate and install the material into the adhesive at the appropriate time – too early will mean air bubbles; too late, a poor bond.
Trowels and adhesive application have always been a concern within the industry. Trowels wear down and do not apply enough adhesive, or they are re-notched and leave an irregular spread and finally, using the incorrect notch leaves either too much or too little adhesive. Rolling the material thoroughly with the proper weighted roller is imperative. It sounds elementary, but is more important than ever.
Porous substrates are more forgiving than non-porous substrates. A porous substrate will provide an avenue for trapped moisture to go. This means the material can be placed into the adhesive while it is still semi dry-to-touch and after a recommended open time. By dropping the material into the adhesive while it is still semi dry-to-touch, the rolling of the sheet material will eliminate adhesive irregularities and flatten out the trowel notch ridges. This will control trowel notch irregularities and help stop indentation concerns.
Installing over a non-porous substrate is much more common than in years past. More concrete slabs have curing and sealing compounds used on them and not removed. And even when an attempted removal is done, the pores in the concrete do not open. There are a lot of moisture mitigation treatments used, some internal in the concrete and some that are applied after the slab is poured. A lot of these are not visible and are hard to detect.
Finally, can a hard-troweled concrete surface with its limited ability to absorb moisture accept an adhesive? Some concrete contractors are guilty of burnishing a slab to a shiny surface, which limits the concrete’s ability to dry properly or to absorb any surface moisture. The best method to determine the porosity of the slab is to broadcast a few droplets of water on the slab’s surface. Watch the droplets to see if they bead up and, over a period of time, soak into the slab. If the water droplet beads up and remains that way the slab is non-porous (non-absorptive). The installer needs to be aware of this condition of the slab and be able to identify it at all times.
Going over cementitious skim coats. Many installation flooring contractors will rely on a skim coat of a patching compound to make the slab absorptive. To be successful, the skim coat must be at least 1/8” in thickness. There is another concern that comes with applying adhesive over a cementitious patching compound: When an adhesive is allowed to dry-to-touch, the pressure sensitivity time of the adhesive is reduced by as much as 50 percent. This pitfall is common among installers and a poor bond is the result.
Rolling out troweled adhesives. Several adhesive and flooring manufacturers have recommended trowel-applied adhesive to be rolled with a short nap paint roller to flatten out the trowel ridges. I have witnessed this recommendation and feel it does help stop the trowel ridge show-through problem. Many installers who have used this method find it works well.
The downside is it takes a little more time, but there are benefits as well: The adhesive will dry-to-touch quicker, and because there is a larger bonding surface than trowel ridges a better bond is achieved. I also see more installers using this method for VCT tile installations. To be successful, the installer must keep the roller clean and prevent it from leaving balls of dried adhesive on the finished spread. An easy way to do this is by keeping the roller wrapped in a piece of plastic to keep the adhesive wet and fresh.
Spray application is the most recent method of applying adhesives for resilient materials. Not a new method for applying adhesive, it has been used for carpet for decades. When used for resilient, there are several concerns: Blowing of debris creating bumps beneath the material’s surface and any unevenness of the spray showing through the material. If those two concerns can be eliminated, then the spray application of adhesive could have a major place in the resilient flooring industry.
Adhesives that are designed to dry-to-touch can be sprayed smoothly and evenly while the likelihood of show-through could be eliminated. Attention will have to be paid to keeping the spray smooth, with special attention paid to spray overlaps. Another advantage is if the spray adhesive can be applied thinly enough, the likelihood of indentations which occur in the adhesive line can be kept at a minimum. Finally, it will get the installer off his knees, saving the wear and tear of crawling.
The proper application of adhesive is still the biggest challenge we face in the resilient flooring industry. There are a lot of hurdles to overcome, but rolling and spraying are growing in popularity and are helping to overcome some of the industry concerns.
Looking for a reprint of this article?
From high-res PDFs to custom plaques, order your copy today!