Tackling the Problem of Underlayment Joint Show-through
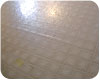
Underlayment joint show-through as a result of the joints being patched.
Underlayment joint show-through is one of the most frustrating problems faced in the resilient flooring industry today. You install an underlayment and resilient material and leave the installation looking great, only to discover within several days that the joints in the underlayment are quite visible and objectionable to the customer. To understand this problem we must look at remodel and new construction aspects of underlayment installation
Remodel or Replacement
In remodel applications it is a little easier to gain control of panel movement problems. These are broken into several categories. Each must be followed precisely to control movement.
Storage: The storage of the underlayment must be in an environment that is similar to the environment in which it will be installed. This means the panels need to be removed from the skids and stored on end to allow air to circulate around each panel. This will allow the moisture content to either increase or decrease to correspond with the humidity of that area. Keep in mind that when underlayment panels are manufactured they have a varying degree of moisture content due to the manufacturing process. Then they are transported, in some cases long distances, from one type of climate condition to another. Many manufacturers and/or distributors will have skids of underlayment wrapped with plastic to protect the underlayment from the elements, but this can also affect the acclimation process. The retailer or installer that goes to either the lumberyard or distributor to pick up the underlayment the day before, or the day of, the installation is asking for an installation failure as there is no time allowed for acclimation.
Acclimation: All underlayment manufacturers recommend underlayments be allowed to acclimate on the job site for 48 hours prior to installation of resilient floor covering. We do this with hardwood flooring, but are reluctant to do this with underlayments; yet underlayments are just as important and susceptible to moisture movement as hardwood. If the underlayment is stored in a shop with a controlled environment it is almost as good as storage at the job site, providing the panels are taken out of the skids and stored on edge.
Moisture testing: Moisture testing should be done with a pin type moisture meter used for testing wood. The subfloor should not exceed 13% and the underlayment should be no more than 3% difference from the subfloor.
Spacing: Depending upon the underlayment manufacture, there are several specifications regarding spacing requirements. This is predicated on the species of wood, the type of lay-up of the wood veneers or chips and the thickness of the specific underlayments. Since the spacing requirements vary so much it is imperative the installer know and follow these requirements. If you do not know the specifications then butt the edges lightly and do not fill the joints. Always allow an expansion zone around the perimeter of the room. Never fit panels tight.
Nailing patterns: There are two important factors involved in the fastening of underlayments. First is the size of the fastener. Whether using a ring, screw shank nail or a staple, the first consideration is length. The fastener should not be longer than the combined thickness of the underlayment and subfloor combined, because when a fastener blows through the subfloor, the holding power (withdrawal resistance) of the fastener is compromised.
Second is the nailing pattern. All underlayment manufacturers have recommended patterns for fastening. These are determined by the thickness of the underlayment panels. You will generally find a closer pattern on panel edges than in the field. Even more important is that the fastener should be kept to within 3/8” of the joint edge to prevent the edges from peaking. In the field, stagger the nailing pattern to prevent a wavy effect in low-level light. The Engineered Wood Association suggests a diagonal fan pattern. The nailing should commence at the corner of the two butted sides and work across to the open sides to prevent any fullness from being nailed into the panels. Each panel should be fastened entirely, before proceeding to the next panel.
Joint treatment: There are many opinions to properly prepare the joints of underlayment panels. I think the underlayment joints should be factory edges, butted lightly and sanded smooth. No patching, unless it is necessary for the occasional joint. When patch is used and an adhesive is applied, the growth of the underlayment will cause the panels to expand and push the patch up. Even though it is only pushed up slightly, it could be enough to show through the finished floor.
Adhesives: Adhesives add water to the underlayment. Your selection of adhesive should also be determined as to the effect it will have on the underlayment. All adhesives manufacturers have specific requirements for the proper trowel notch for application of their adhesive over porous floors and underlayments. Equally important is proper open time. Open time allows the moisture to start to evaporate off the adhesive, and allows the adhesive to develop body rather than letting the moisture be trapped under the material. This forces the moisture into the underlayment, causing the wood fiber in the underlayment to expand.
In residential remodel situations, often the underlayment is over an existing material or materials. These materials are effective vapor barriers, preventing the moisture migration from beneath the underlayment. If you are seeing moisture problems, chances are moisture must have been introduced into the underlayment during the installation phase. Give thought to the following:
• The way the underlayments are stored.
• If adequate time is given for acclimation.
• Have you recorded the moisture test results for both the underlayment and substrate?
• The method used to fasten underlayment panels to the substrate.
• All joints are sanded smooth, no ledging between panel joints.
• If the adhesive is applied with the proper notched trowel and adequate open time is given to the adhesive.
Ask yourself if you have eliminated all possibilities of excessive moisture from being absorbed into the underlayment.
Looking for a reprint of this article?
From high-res PDFs to custom plaques, order your copy today!