Custom pitches in on Marlins Park baseball stadium
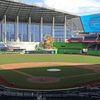
Crews are hard at work putting the finishing touches on Marlins Park, the $515 million ballpark that is the new home of Major League Baseball’s Miami Marlins, to ensure that it is ready for Opening Day against the St. Louis Cardinals on April 4. Located less than two miles from downtown Miami on part of the historic 42-acre site of the former Orange Bowl stadium, the facility features a retractable roof, a natural grass playing field, 37,000 seats, 28 luxury boxes, and over 175,000 square feet of quarry, porcelain, granite, ceramic and glass mosaic tile.
Tile and stone are used in virtually every area throughout the ballpark, including concession areas, corridors, restrooms, walls, locker rooms and showers, executive floors, and decorative walls and pillars. With over 175,000 square feet of tiled surface, it represents one of the largest installations ever completed by Artisan Tile and Marble of Jupiter, Fla., who was awarded the contract for the entire tile project and partnered with Custom Building Products for all installation products.
“We knew that everyone in the Southeast wanted this project, so we had to be extremely competitive in our approach in order to win the business,” said Chris Drehmann, vice president of Artisan. The original architectural specifications for the project included a wide range of products from numerous suppliers, but Drehmann believed that partnering with a single provider on a project of this size could mean better technical support, improved efficiency and greater cost effectiveness.
“We did an analysis of the project requirements against various suppliers. Custom worked with us to put a package together that not only met the specifications, but also helped us value-engineer the project so that we were able to get the best price per square foot and meet the ever-challenging budget requirements. We couldn’t be happier with the result. They were a true partner every step of the way,” he added.
CEG-Lite Commercial 100% Solids Epoxy Grout was used on flooring throughout the massive structure, and Custom’s technical representatives were on-hand to train Artisan’s crews on the products and help facilitate the installation throughout the entire two-year project.
The first phase of the project was setting abrasive quarry tile, one of the most difficult types of tile to grout. Patty Velez, territory manager for Custom in South Florida, worked directly with Artisan, training the tile crews on CEG-Lite and EBM-Lite Epoxy Bonding Mortar.
Other Custom installation products used during the project included: LevelQuik RS (Rapid Setting) Self-Leveling Underlayment, RedGard Waterproofing and Crack Prevention Membrane, Medium Bed Mortar, ProLite Tile & Stone Mortar, Prism SureColor Grout, Polyblend Grout and Aqua Mix Penetrating Sealer.
The sheer size and scope of the two-year project presented unique challenges in managing product resources. While the size of the facility is very large, there were no storage provisions for product, so Custom and Artisan worked together to anticipate product needs and maintain a consistent, timely flow of product deliveries in order to maintain the unforgiving schedule. According to Drehmann, support from Custom was essential and helped the installation remain on pace.
“Opening Day is Opening Day,” said Drehmann. “There was no room in the schedule for error, and Custom’s team of experts helped us stay right on track, with no delays or setbacks. I have never seen a project of this scope go so smoothly. We are really proud of this one, and can truly say it was a team effort from start to finish.”
Looking for a reprint of this article?
From high-res PDFs to custom plaques, order your copy today!