Contractor Roundtable: Subfloor Prep








It is essential to properly prepare the subfloor to ensure a successful installation. Every situation is unique and will have its own prep requirements. We asked flooring contractors to discuss the strategies and products they use for careful and correct preparation.
Our roundtable included Josh Dorman, sales territory manager of Corporate Floors in Rochester, N.Y., and owner of the installation firm Dorman Flooring; Fritz Hoehn, owner of Atkinson Carpet Installation in Haverhill, Mass.; Tim Newman, president of Accu Flow Floors in Barrington, Ill.; Ron Fenhaus, vp sales, at Action Floor Systems in Mercer, Wis.; Joshua Reed, operations manager concrete prep and coatings division for The Rouse Company in Rancho Dominguez, Calif.; and Bob Seman, president of Seman Floor Leveling System in Washington, Pa.
FT: What are the most common issues you see with subfloors and subfloor prep?
Dorman: The most common issues we run into are high moisture readings and chemical abatement projects that leave chemical residue in concrete that slowly eat away adhesives.
Fenhaus: We specialize in sports flooring systems and we often see inadequate preparation of the concrete slab. Sometimes we will see low or high spots, areas poorly filled, and construction residue that has not been scraped or ground off of the slab surface, all of which can telegraph through vinyl or urethane installed athletic flooring. This can result in poor aesthetics for the finished floor. At times concrete can curl at the cut joints, so joints should be ground flat in advance of installs as well. Lastly, concrete sealers used as curing agents have been known to inhibit the floor system’s adhesive from bonding to the slab.
Hoehn: We are located in the Northeast and have to deal with a few conditions that we come across on a regular basis. For starters, we are working in buildings that are sometimes up to 150 to 200 years old. In those years they’ve had multiple flooring replacements, so we have to deal with getting the old products out, both materials and floor prep materials—a lot of which have not been done properly. They have not used premium products, so it’s really a mess when we get into it. Plus, a lot of the buildings around here have used low-cost gypcrete in their renovations over the years and it’s low quality. It takes a lot to get those floors prepped right when gypcrete is down.
Also, here in the Northeast we’re dealing with changing weather conditions. We have everything from extreme cold to heat and humidity—and sometimes both in one day. When you combine climate variations like that, combined with older buildings, you get a lot of movement in the buildings, particularly in the floors. You need to adapt quickly, and equip your installers properly, in order to address subfloor conditions on projects.
Newman: The most common issues I run into with the subfloors and prep is making sure to diagnose what is on the floor, finding out if it is bonded and if it can be poured over, and choosing the correct Ardex product. Sounding the floor with a golf ball or chain dragging to listen for hollow spots and removing those areas prior to pouring.
Reed: The most common issue we run into with subfloors is that they require some type of unforeseen prep. The most common type of prep we run into is the necessity of achieving specific elevation points throughout a floor or a particular space.
Seman: Everybody overlooks adhesive removal. A big percentage of the floor covering patch and prep that gets done is put over contaminated surfaces. So, the bulk of the installers that don’t know the proper way are going in and maybe not even vacuuming; they’re sweeping the floor and they’re putting floor patch right over old adhesive and construction dust and dirt.
FT: Please share an anecdote of a job you’ve had where you had a subfloor problem that had to be rectified, and the solutions you came up with.
Dorman: Mount Pleasant Cottage Schools in Thornwood, N.Y., had an athletic sports floor installed over top of existing wood parquet floor because school didn’t want to pay for demo and check for asbestos. The wood swelled from severe moisture in the concrete slab, making large waves in floor and creating an unsafe floor. Our biggest challenge was time on this project because we had a short window to get the work done while kids were out of school. We had a solution after we received news that there was no asbestos in the flooring. Pull back athletic flooring one half of the way and do the following process: demo wood, grind all adhesive off concrete slab, apply epoxy moisture control (Schönox EPA), prime (Schönox SHP), pump leveler (Schönox US), install that half of gym. Repeat all steps for second half.
Hoehn: In 2014 we had a project at a school in Billerica, Mass. The building was built during the 1950s. They installed a floating hardwood system over a 2”-thick dry pack of sand and dirt. The product was failing because of moisture and because of the dry pack dissolving due to termite infestation. The floor was buckling, so we had to go in and manually rip up the wood. We used a ride on ripping machine to rip up the dry pack. Then we shot blasted the floor, did an Ardex moisture mitigation system, along with an Ardex self-leveling system. Lastly, we installed a new VCT floor and it has worked out great for the client.
Newman: In one project, the gypsum substrate had to be 1/8” in 10 feet of tolerance because it was getting custom wood and cabinetry. It was at least 1-1/2” low in the middle and at grade at most of the perimeter windows. It was shot with a laser for elevations, lightly machined, primed with Ardex P-51 then barrel mixed with Ardex K22 F self-leveling underlayment, which is fiber reinforced.
Reed: On a project we completed last year in Thousand Oaks, Calif., there was a subfloor that was depressed in an area and heavily cracked. The rest the space was substantially deflected and outside of the wood flooring requirements. To help the bond and keep the cracks from telegraphing through the finish floor in the depressed area we installed TechPrime E and broadcast sand to refusal. We then poured TechLevel 150 to fill the depression. The rest of the space was bead blasted, primed with TechPrime A and leveled with 3/8” average of TechLevel 150.
Seman: Just yesterday, an office was being retrofitted. The new office was bigger than the old office and part of a warehouse space was being used. There was a floor drain in the warehouse, so half of the office had a heavy slope to it right where the desks would sit. So we had to fill that low area with the Ardex self-leveler before we could put the sheet vinyl flooring on it. This particular job, I noticed the problem in the estimating, so I was able to plan for it. Since I do a lot of subfloor prep, I’m in tune to looking and trying to find a problem before it’s a problem.
FT: What types of floors require a flat subfloor?
Hoehn: Any hard surface products really need a flat subfloor, especially click, or snap-together, LVT products. With soft surfaces, having a flat subfloor is not as critical, but still important on specific projects and what the end user will be using the space for.
Fenhaus: Both the flatness and quality of the slab are critical for the installation of a sports floor system to be successful. Improper preparation, unevenness or undulation of the slab can impede the uniformity of the playing surface. These can lead to many things, from player injury to changed ball direction during a game, and will negatively affect the immediate and long-term satisfaction of the owner with the finished product.
Dorman: Almost all floors require flat subfloors but some more than others. We are able to accomplish giving the customer a much flatter/smoother floor by using Schönox products. We are able to save on labor costs because of how installer friendly Schönox products are.
Newman: There are all types of floors that require a flat substrate such as large-format hard surface ceramic tile, stone floors, certain wood and others that don’t allow much adjustment with certain glues and setting materials. There are others that require even more of a tight tolerance or flatness such as TV studios and hospital MRI rooms that have to be super flat. By working hand in hand with Chris Nathe, who is the head Ardex sales representative in Chicago, together we have been able to come up with a solution for all flooring needs.
Reed: To a degree, every floor we install requires a flat subfloor. Even carpet over pad in severe cases would require a certain amount of prep to achieve a flat enough subfloor. The majority of floor prep that we end up doing is likely related to our wood floor installations that typically require a 1/8” or 3/16 in 10’ tolerance.
Seman: A big portion of our business is subfloor prep and leveling. Large format ceramic tiles have been what’s driving a lot of our work right now. For these, the floor needs to be very flat so that there’s not ledging. If you have an uneven floor, the large porcelain tiles will crack. It’s a very common thing for those tiles to crack. So, we’ve been leveling for large format tile and we also do leveling for hardwood floors because those floors need a tight tolerance. We also do leveling in hospital environments for sheet flooring.
FT: What are your go-to products for common subfloor problems?
Hoehn: We only use premium products such as Ardex, Schönox and Chapco subfloor conditions. Each of those manufacturers have products that work really well for a variety of subfloor conditions. For example, Ardex’s Feather Finish product works well for small cracks and imperfections in the floor. It creates a smooth, flat surface for installation and our installers love working with that product.
Fenhaus: Generally, moisture issues can be resolved with an upgraded sheet-type vapor barrier or a topically applied moisture barrier that works with the floor system, whether a vinyl or urethane sport floor product. Because of the challenges and potential liability that come with addressing asbestos, we recommend owners contract a licensed asbestos firm to properly remove and dispose of any asbestos in the facility’s flooring. Cement-based leveling and patching materials are preferred, as they adhere well to the concrete and typically work well with the adhesives used. Small cracks generally do not impede the installation process and can easily be corrected using urethane fillers in problem areas.
Dorman: For high moisture and chemical abatement residue, we use Schönox EPA. For high moisture / chemical abatement residue with fast turnaround, Schönox EPA Rapid. For skim coat material, Schönox SL. To achieve extremely flat subfloors, we use Schönox AP because it’s extremely fluid.
For fast turn-around for installation we use Schönox ZM Rapid. The Schönox products are cost effective and almost all of their levelers/patches are moisture and pH resistant, which is huge for us because we run into moisture problems all the time.
Newman: There are a lot of concrete slabs that have high moisture content these days and require a moisture mitigation system to keep the levels acceptable for a quality flooring installation. Ardex’s MC Rapid takes care of the problem with shot blasting the concrete, installing the MC Rapid and either priming and installing a product, such as Ardex V -1200, or sanding into the MC and pouring over it to get it ready for finished flooring. If we see cracks in the concrete we like to use Ardex Ardifix which is their crack repair epoxy. Our go-to products are Ardex V-1200 for over concrete, K22F, which is fiber reinforced over gypsum, Liquid Backer Board over wood and SD-T and PCT, which are toppings. If we run into any asbestos floors, we like to have them abated prior to pouring over it. Between pouring over wood, concrete, tile and other substrates and working in tandem with Chris Nathe, we are to make any floor flat and ready for flooring.
Reed: The products we require for prep have as much to do with the type of flooring being installed as the condition of the subfloor. With resilient flooring over a typical concrete floor we often require the use of a moisture barrier or at a minimum good skim coat materials. With our wood flooring installations we typically have to use self-leveling cements for prep.
Seman: Our go to products are Ardex’s MC Rapid vapor control and their K 60. K 60 is a miracle in a bag. It’s very forgiving because the powder is mixed with a latex additive. There’s no other product on the market like it.
Tools of the Trade
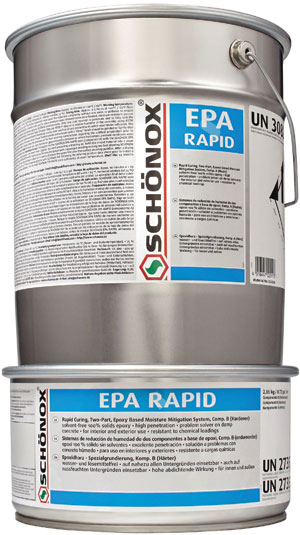
Schönox EPA Rapid
Schönox EPA Rapid, a fast curing moisture mitigation system, was made for time-sensitive retail installations with moisture problems. It has already saved untold numbers of renovation and development efforts and kept them moving on schedule. It addresses 100% relative humidity scenarios and dries in as quick as two to three hours. It complies with tough South Coast air quality standards and is solvent free. Schönox EPA Rapid is solving moisture issues with speed and environmental performance.
hpsubfloors.com
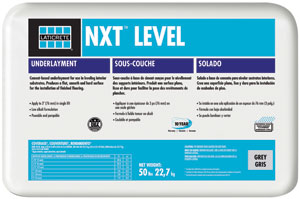
Laticrete
Laticrete NXT Level is a cement-based underlayment for use in leveling interior substrates including concrete, vinyl tile, cement terrazzo, exterior glue plywood, cement mortar board, cement backer board, ceramic tile and stone. NXT Level produces a flat, smooth and hard surface for the installation of finished flooring. The formula is a factory-prepared blend of cement, aggregate and other materials to produce a flowable, fast hardening underlayment that can be distributed via pour or pump. Common applications include interior thin bed floors and renovations.
laticrete.com
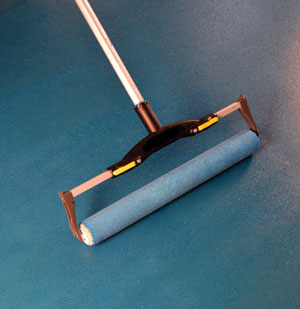
Ardex VR 95
Ardex VR 95 Fast-Track, One-Component Moisture Vapor Retarder is a ready-to-use, one-component, water-based, two-coat system formulated to suppress residual moisture in new concrete with RH readings up to 95%. Ardex underlayments may be installed over the second coat in as little as 2 hours without priming. ARDEX VR 95 comes in a ready-to-use, resealable container. It is pigmented blue to help indicate uniform coverage for ease of application.
ardexamericas.com
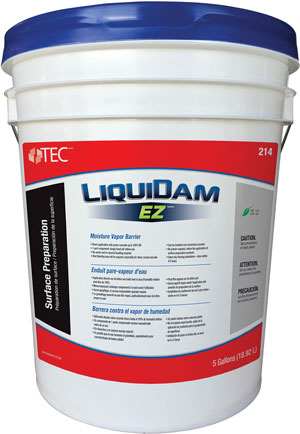
TEC LiquiDam EZ
TEC LiquiDam EZ is a high-performance, single-component, liquid-based moisture vapor barrier. Formulated to be used on damp or new concrete up to 100% RH, LiquiDam EZ allows for same-day floor installation. The barrier is colored blue for visual assurance of coverage during the application process. Two coats are required to fully seal the substrate; and it quickly dries in as soon as 4-5 hours.
tecspecialty.com
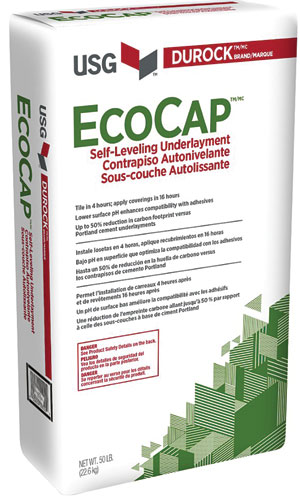
USG Durock EcoCap
This eco-friendly, self-drying, cement-based underlayment is used over concrete and wood subfloors. Mixed with water at the job site, this product allows installation of ceramic tile and natural stone in four hours and other floor coverings in 16 hours. Offers superior crack resistance due to low shrinkage, thermal stability and exceptional bond.
usg.com
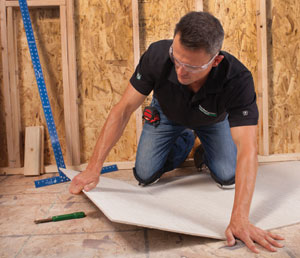
HardieBacker Cement Board
HardieBacker cement board is a mold-resistant underlayment specifically designed for walls, floors and countertops in wet areas like bathrooms and kitchens. Available in 1/4-inch and 0.42-inch thicknesses, as well as 3x5-ft and 4x8-ft boards. It is comprised of 90% Portland cement and sand; cuts cleanly with sharp edges for tight seam lines; features excellent tile adhesion and passes both ASTM mold and mildew resistance tests with perfect scores.
hardiebacker.com
Looking for a reprint of this article?
From high-res PDFs to custom plaques, order your copy today!