Mortar Bed Installation
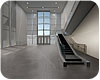
Mortar beds seem to be making a resurgence with the increased use of large tile. It’s a little ironic to me that after almost 40 years of industry realignment caused by the invention of thinset, we are back to a method that has worked for thousands of years and is still the predominant method used in many countries. With the popularity of large size tile and small grout joints, very few substrates are suitable for direct application of tile without additional remedial measures to flatten out the floors.
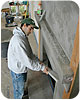
Thinset is an expensive and inappropriate material used for this purpose more often than we would like to see. Thinset products are designed as bonding materials. With a standard thinset the maximum bonding thickness should never exceed 3/8 inch. If something is classified a medium bed mortar it is typically good for a maximum bonding thickness of ¾ inch. The problem with applying thinset that thick from an installer perspective is that you are going to be using a lot of mid-price-range bonding material. This is a great money maker for setting material manufacturers, but bad for the profits of the tile person, as typically you don’t know in advance what the flatness conditions are going to be. Self-leveling products, a misnomer if there ever was one, are also a possibility. However they tend to be very finicky about prep prior to application and cost wise, in our shop we referred to it as pouring dollars out of a bag. Most are also adverse to moisture so damp floors and wet areas are a further consideration. When possible, sometimes the best thing to do is also the least expensive: just mud it!
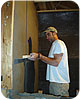
Today’s wooden structures do not readily lend themselves to mortar bed installations. Thickset or mud installations can be quite heavy. One inch of mortar weighs approximately 12 pounds per square foot. Most of our current code compliant residential structures allow 10 pounds per square foot as the weight of the entire structure. Very few mortar beds are only an inch in thickness; most range in the 1 ¼” to 2” range plus the weight of the tile. This type of installation system would easily require a minimum of an additional 20 pounds of load carrying capacity be added to the structure. To use an example: if you were to have a 2x10 floor joist in a normal residence on 16” centers, to meet the L/360 criteria of building code and tile installation, the maximum length could be 16’. If you were to “beef-up” the floor system to handle a mortar bed, that length would now become 13’5”. Older homes, those built prior to the 1970s roughly speaking, tended to be what we would call over-built in today’s market. The reasons for this change are both in the wood products available and the desire to be ecologically friendly and value engineer today’s homes. The home building market has evolved to the point where it is all about dollars and cents; as anybody in construction knows, though, there can be some exceptions. Many if not most wooden structures constructed today will NOT accommodate a mortar bed installation without substantial reinforcing of the supporting floor system.
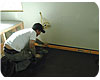
So just exactly what is this mortar we keep referring to? There are several terms to describe mortar work for tile. The most common is deck mud or dry-pack for floors and fat mud for walls. The first reaction most people have when they see and feel the consistency of mortar used for floors, countertops and benches is “that looks way too dry!” Floor mortar, commonly called deck mud, is probably not what you might expect if you are used to seeing concrete, brick mortar or stucco. All these materials use Portland cement, aggregates and typically water to begin a chemical reaction. Most of these cement products use what is called water of convenience. That means that more water than is necessary is used to provide ease of placement such as emptying a concrete truck or building a brick wall. In tile work, for ease of placement, an optimum amount of water is used, no more than necessary to start the chemical reaction. That allows for the material to be easily moved around the substrate as need in a fashion similar to that of building a sand castle, just enough water to hold its shape. Deck mud is not poured but rather placed. Excessively wet deck mud cannot be compacted because the moisture in the mix acts like a lubricant and creates more space between the aggregate particles.
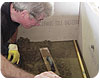
The original design of mortar installations was to provide a substrate and means of bonding ceramic tile. Today deck (floor or dry-pack) mud is used to produce flat or sloped setting surfaces for ceramic or stone tiles. It is especially helpful to produce flat surfaces for very large unit tile. Sometimes a wire reinforced mortar bed and cleavage membrane is used over a plywood subfloor; sometimes it is used to over concrete. Installations over concrete offer the additional option of directly bonding the mortar to the slab without reinforcement. Methods of installation are varied depending on the structure in addition to the needs and performance attributes desired. There are various methods for floating mortar beds, bonded mortar beds, roof decks, wet area applications and wall installations. Deck mud can be used for residential or even extreme service industrial installations depending on the level of compaction applied to the mud.
The best deck mud is the result of three things: the right combination or ratio of ingredients, proper mixing and compaction. For all mortar applications the sand should be clean, sharp and slightly damp. Rounded sand grains offer only a fraction of the compressive strength achieved with sharp sand. Think of trying to pack a bunch of round golf balls in a box as opposed to a bunch of diamonds with their flat surfaces. Flat surfaces on the sand offer much more compactness and greater strength as well as easier handling. The proper mix ratio is determined by the installation application.
In some instances a latex additive is used in a mortar bed when low porosity or high strength is required. Use of latex additives in mortar beds can produce a dense material much harder than most concrete. However, when using a latex additive, the mortar bed must be protected from exposure to additional moisture and allowed to thoroughly cure before water emersion. In the case of swimming pools or other equally wet environments this can be 14 to 21 days. When mixing with plain water, dependent on application, a sand/cement ratio between 6/1 and 4/1 is typically recommended for floors. Mixtures too “rich” in cement are prone to cracking and excessive shrinkage. On the other hand not enough cement yields a soft deck mud with very little compressive strength. My experience, as echoed by any other tile setter I have ever worked with or spoken to, says you will always need to tune the mix ratio based on the cement and sand available in your area; materials vary greatly in a given geographic area. There are many ways to mix mortar and none are right or wrong, as long at it is thoroughly and properly mixed. On large installations, transit trucks, gas and electric powered mixers and even roto-tillers have been used to mix both floor and wall mud. Regardless of the method used, mixing must be complete enough for all the ingredients to become homogenized. One type of mixer that does not work is a concrete mixer. Mortar mixing needs a blade or paddle type configuration.
All of this is good information but still no mention of exactly how to do it. Well, the skills of working with mortar work are similar to riding a bicycle; once you master it, it comes naturally. What does not come so easily is all the little knowledge-based nuances like: acceptable wire reinforcing; how the wire is placed and/or attached; what is the right mix; and how to get it flat. A good source of information on varied mortar related subjects is the Ceramic Tile Institute of America Field Reports available for review at www.CTIOA.org. You can find more information on such subjects as Portland Cement, Aggregates, and Water; Portland Cements, Lime and Sand; Reinforcing Wires for Mortar; Expanded Metal Lath and Wire; and Working With Portland Cement. The Tile Council of America Installation Handbook (www.tileusa.com) has numerous details for both interior and exterior mortar applications such as decks, showers, countertops and swimming pools. Material requirements for mortar beds are contained in the American National Standards for Ceramic Tile Installation (ANSI A-108) where you will find reference to the types of wire acceptable, sand to cement ratios, cleavage membranes, and other mortar work related items. None of these documents serve as instruction manuals, but with common sense and a little help from someone experienced, a dedicated tile setter can figure it out.
See more installation news and features
Mortar work is not difficult to master; it just takes some basic knowledge of sand and cement and a lot of time to practice. Those who do learn tend to have a life-long preference to do mud work. Given the shortage of mud mechanics (yes, a technically knowledgeable person in a manual trade makes you a mechanic), wages tend to be higher than those who do thinset methods exclusively. The success stories of those who attended the CTEF mortar shower courses and mortar floor and wall basics are numerous and in some instances amazing to me. A long time mud man, John Bridge at johnbridge.com, has also put together a mortar course to be held mid September in Dallas, TX, and hosted by Laticrete for those interested. The opportunities are there and the money is pretty good; maybe you should give CTEF or John Bridge a try and broaden your horizons a little.
Looking for a reprint of this article?
From high-res PDFs to custom plaques, order your copy today!