Indentation Nation: How a Dent Makes Its Mark
It is amazing how many times I look at a flooring issue at a hospital, and end up hearing the same concerns I have being expressed by the staff.

It is amazing how many times I look at a flooring issue at a hospital, and then hear the same concerns expressed by the staff.
The flooring material is relatively smooth with multiple coats of high-gloss polish. You talk to the hospital staff and they have no idea how much a high-gloss finish will accentuate even the slightest irregularity in the material, adhesive or substrate. Their only concern is how shiny the surface of the floor is. And at almost any hospital you’ll find a huge amount of low-level light, which exacerbates the whole issue.
End-users are hung up on the static load capabilities of a piece of material. The mentality is “the higher the number, the better the material.” They do not take into account the effect that foot traffic, equipment, rolling loads and stationary loads have.
All materials indent; the question is, to what degree it will indent? The industry standard is that an indentation up to 0.005-inch is acceptable. But if you look at a 0.005-inch indentation, it is extremely visible in a high-gloss, low-level light environment. Where is the indentation taking place? Is the indentation in the material, the adhesive or in the substrate? What is causing the indentation: heavy equipment, hospital beds, static or dynamic loads, or foot traffic?
High-Gloss Finishes: It is hard to determine why this high-gloss, mirror-like appearance got its start, but I have seen floors with up to 15 coats of a high-gloss polish buffed to a mirror-like finish.
In one instance I encountered a floor with a thick build-up of polish and the hospital staff was complaining that the chairs were indenting the material. After the use of a strong floor stripper to remove this high build-up of polish, the staff realized the indentation was in the floor finish, not the material.
After the removal of the high-gloss polish, the surface of the material had a reduced gloss level. Maintenance personnel need to understand that two or three thin coats are better than one heavy coat of polish. Many hospital chains are realizing that a lot of their problems with indentations can be eliminated by going to a lower-gloss polish system.
Materials: It takes a lot to indent a piece of homogeneous or heterogeneous material. When a piece of material is sent to be tested for static load capability, they rarely fail to pass. The reason is the indentation is not occurring in the material, but in the adhesive or the substrate.
The next thing is that when an indentation is close to the maximum it looks extreme. If you were to look at the difference in the depths of indentations, you would find that a 0.001-inch indentation is not very noticeable, but a 0.005-inch indentation looks like a crater.
Adhesives: The adhesive is where most of the indentations are occurring. In a fine-notch trowel application, the adhesive film is about 1/32-inch deep when applied, then allowed to dry-to-touch. The material is placed into the adhesive and rolled with a 100-pound roller, and the remaining adhesive film is, depending upon adhesive, still around 0.018-inch – 0.022-inch.
This means that the likelihood of an indentation appearing
in the adhesive line is very high, especially if the adhesive is not cured.
Finding an adhesive that fulfills this need is difficult. If an adhesive is too
hard, the installer needs to be very careful on the use of the trowel because
the trowel notch or any irregularities in the adhesive spread will show through
the finished material.
If the adhesive is too soft, the possibility of indentation is severe. The same is true of the trowel notch; trowels that are not properly notched will make the material prone to indentations. Not only the depth of the trowel notch but the spacing as well. Flooring and adhesive manufacturers have tried several methods to stop this problem from occurring. Rolling the adhesive with a paint roller does not work very well because it is difficult to maintain a uniform adhesive film. This would allow indentations in the areas where the adhesive film was too heavy.
Back rolling the adhesive with a short-napped paint roller after the adhesive has been troweled. This method works well in knocking down the trowel ridge. With a hard-setting adhesive, trowel notch show-through is kept a minimum because, while the trowel notch is essentially gone, since it was troweled, the adhesive film is relatively uniform.
Spraying the adhesive is one of the newer methods being used to try to eliminate the indentation problem. The spray can be applied in a very thin film and it keeps the indentation from developing; unfortunately, a thorough cleaning of the substrate is a must.
Dust and fine dirt, either on the back of the material or on
the floor, can work as a bond breaker and lead to other problems. The sprayer
can also kick up debris and get beneath the material, creating a show-through
of the material. The application of the spray must be uniform and, if it is too
heavily applied, can also result in either an indentation problem and/or a
lumpy show-through.
Application of an adhesive film to the back of the material is the latest attempt to overcome the indentation problem; it is believed that a film of adhesive less than 5-mils will eliminate the indenting at the adhesive line. In these cases the adhesive would have to be pre-applied to the materials back and covered with a release paper. Like the spraying method, dust on the substrate would have to be controlled with the use of a primer.
Moisture Problems: Marginal moisture conditions are also a concern. For example, when an installation is started when the moisture is on the upper limit of the moisture specification. The adhesive will remain soft and not totally cured and for how long remains to be seen. Soft adhesive film and indentations go together.
Hospital Equipment and Beds: The manufacturers of hospital equipment have no concerns for the flooring industry. The casters on some hospital beds are rounded instead of flat and leave a very small foot print (static load pattern). This small footprint, coupled with the weight of the bed (and of a patient) is enormous. Lock this caster down and get it to pivot while locked, and the possibility of an indentation is extreme.
The real solution to this problem is to control the amount of adhesive applied to the substrate, and use a polish that is a low-gloss or matte finish. The hospital bed problem will remain until we get some cooperation from the bed manufacturers. Epoxies are not the answer.

It is amazing how many times I look at a flooring issue at a hospital, and then hear the same concerns expressed by the staff.
The flooring material is relatively smooth with multiple coats of high-gloss polish. You talk to the hospital staff and they have no idea how much a high-gloss finish will accentuate even the slightest irregularity in the material, adhesive or substrate. Their only concern is how shiny the surface of the floor is. And at almost any hospital you’ll find a huge amount of low-level light, which exacerbates the whole issue.
End-users are hung up on the static load capabilities of a piece of material. The mentality is “the higher the number, the better the material.” They do not take into account the effect that foot traffic, equipment, rolling loads and stationary loads have.
All materials indent; the question is, to what degree it will indent? The industry standard is that an indentation up to 0.005-inch is acceptable. But if you look at a 0.005-inch indentation, it is extremely visible in a high-gloss, low-level light environment. Where is the indentation taking place? Is the indentation in the material, the adhesive or in the substrate? What is causing the indentation: heavy equipment, hospital beds, static or dynamic loads, or foot traffic?
High-Gloss Finishes: It is hard to determine why this high-gloss, mirror-like appearance got its start, but I have seen floors with up to 15 coats of a high-gloss polish buffed to a mirror-like finish.
In one instance I encountered a floor with a thick build-up of polish and the hospital staff was complaining that the chairs were indenting the material. After the use of a strong floor stripper to remove this high build-up of polish, the staff realized the indentation was in the floor finish, not the material.
After the removal of the high-gloss polish, the surface of the material had a reduced gloss level. Maintenance personnel need to understand that two or three thin coats are better than one heavy coat of polish. Many hospital chains are realizing that a lot of their problems with indentations can be eliminated by going to a lower-gloss polish system.
Materials: It takes a lot to indent a piece of homogeneous or heterogeneous material. When a piece of material is sent to be tested for static load capability, they rarely fail to pass. The reason is the indentation is not occurring in the material, but in the adhesive or the substrate.
The next thing is that when an indentation is close to the maximum it looks extreme. If you were to look at the difference in the depths of indentations, you would find that a 0.001-inch indentation is not very noticeable, but a 0.005-inch indentation looks like a crater.
Adhesives: The adhesive is where most of the indentations are occurring. In a fine-notch trowel application, the adhesive film is about 1/32-inch deep when applied, then allowed to dry-to-touch. The material is placed into the adhesive and rolled with a 100-pound roller, and the remaining adhesive film is, depending upon adhesive, still around 0.018-inch – 0.022-inch.
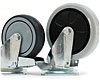
If the adhesive is too soft, the possibility of indentation is severe. The same is true of the trowel notch; trowels that are not properly notched will make the material prone to indentations. Not only the depth of the trowel notch but the spacing as well. Flooring and adhesive manufacturers have tried several methods to stop this problem from occurring. Rolling the adhesive with a paint roller does not work very well because it is difficult to maintain a uniform adhesive film. This would allow indentations in the areas where the adhesive film was too heavy.
Back rolling the adhesive with a short-napped paint roller after the adhesive has been troweled. This method works well in knocking down the trowel ridge. With a hard-setting adhesive, trowel notch show-through is kept a minimum because, while the trowel notch is essentially gone, since it was troweled, the adhesive film is relatively uniform.
Spraying the adhesive is one of the newer methods being used to try to eliminate the indentation problem. The spray can be applied in a very thin film and it keeps the indentation from developing; unfortunately, a thorough cleaning of the substrate is a must.
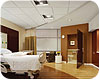
Application of an adhesive film to the back of the material is the latest attempt to overcome the indentation problem; it is believed that a film of adhesive less than 5-mils will eliminate the indenting at the adhesive line. In these cases the adhesive would have to be pre-applied to the materials back and covered with a release paper. Like the spraying method, dust on the substrate would have to be controlled with the use of a primer.
Moisture Problems: Marginal moisture conditions are also a concern. For example, when an installation is started when the moisture is on the upper limit of the moisture specification. The adhesive will remain soft and not totally cured and for how long remains to be seen. Soft adhesive film and indentations go together.
Hospital Equipment and Beds: The manufacturers of hospital equipment have no concerns for the flooring industry. The casters on some hospital beds are rounded instead of flat and leave a very small foot print (static load pattern). This small footprint, coupled with the weight of the bed (and of a patient) is enormous. Lock this caster down and get it to pivot while locked, and the possibility of an indentation is extreme.
The real solution to this problem is to control the amount of adhesive applied to the substrate, and use a polish that is a low-gloss or matte finish. The hospital bed problem will remain until we get some cooperation from the bed manufacturers. Epoxies are not the answer.
Looking for a reprint of this article?
From high-res PDFs to custom plaques, order your copy today!