How to Avoid Failures on Balcony and Roof Deck Tile Installations

Photo: Getty Images.
Many projects encountered by tile installers involve water management where the only requirement is to direct the water to where it belongs. Unfortunately, when water is not managed appropriately, the results are less than stellar and almost always result in failure. This is the case with the installation of tile or natural stone on an exterior roof deck or balcony, which in and of themselves, are problematic.
To be successful, these exterior installations require that all the components be installed per the ANSI Specifications, Tile Council of North America (TCNA) Handbook methods, and manufacturer’s instructions. Although this is not a comprehensive list of job requirements, there are several critical items necessary for success. The Handbook lists four roof deck or balcony methods, but for this discussion, we will focus on method F104, above ground concrete slab which is excerpted here.
Recommended Uses
- For exterior balconies or decks of concrete over unoccupied space where waterproof roof membrane is not used, where slab is sloped minimum ¼” per foot, and where thin-bed installation of tile is desired.
Membrane Options
- A waterproof membrane (A118.10) may be specified to prevent moisture intrusion. Specifier shall indicate if complete waterproofing is required, including if/how membrane connects to drain assembly, if base flashing is required, and treatment at other termination points.
- Check with membrane manufacturer for suitability for applicable conditions, as not all membranes are suitable for exterior use or use over above-ground structural slabs.
Requirements
- Slab to be well cured, dimensionally stable, and free of cracks, surface laitance, waxy or oily films, curing compounds, and other surface bond-inhibiting contaminants.
Preparation by Other Trades
- Slope slab minimum ¼” per foot. Flat deck with poor or no drainage will not perform well.
- Slab to have steel trowel finish with no curing compounds used. When used, mechanical scarification is necessary.
Movement Joint
- The architect must specify type of joint and show location and details on drawings.
- Movement joints - mandatory in accordance with EJ171. For above-ground installations, additional movement joints are required.
Mortar Coverage - ANSI A108.5
- 2.2.2 Apply mortar with flat side of trowel, keying in with pressure, over an area no greater than can be covered with tile before the mortar skins over. To obtain a setting bed, use a notched trowel of type recommended by mortar manufacturer, comb with the notched side of the trowel in one direction. Cover surface uniformly with no bare spots and with sufficient mortar to ensure a minimum mortar thickness of 3/32 in. (2 mm) between tile and backing after tile has been forcibly embedded. Tile shall not be applied to skinned-over mortar.
- 2.2.3 Contact area on all exterior installations or interior wet installations shall not be less than 95%.
Also, keep in mind: except for Handbook method F105, Structural Ribbed Self-Supporting Boards (SRSB), which has extremely specific requirements, there are no methods for exterior balconies or roof decks utilizing a wood structure or substrate.
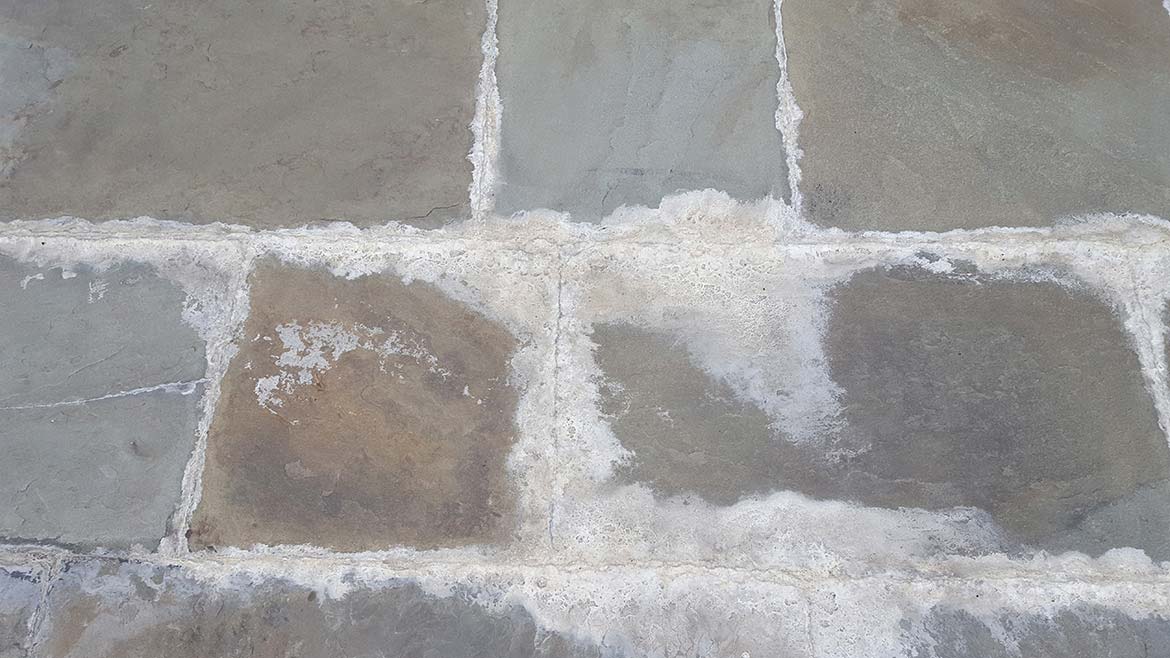
Finally, use extreme caution when considering the installation of tile or stone on a roof deck or balcony. As seen in the attached image, the exterior slate tile installation broke all the rules. The wood substrate was not sloped, there was a low spot in the middle of the span, the mortar coverage was significantly less than the required 95%, there were no movement accommodation joints, and no temporary protection was provided to keep the significant precipitation, which occurred immediately after installation, from compromising the mortar.
Research your options, fully understand what a manufacturer requires and what it will guarantee, recognize your liability, and consider your risk factor. Think about it before you sign any contract.
See more articles from our February 2024 issue!
Looking for a reprint of this article?
From high-res PDFs to custom plaques, order your copy today!